HORN and INDEX demonstrate their joint technology and solution competence.The focus is on five selected processes: High-speed whirling, skiving, spiral bevel gear cutting, grooving and polygon turning. Nowadays, modern INDEX turning/milling centres, in combination with the correct cycle and the right precision tool, offer improved and new possibilities or approaches to optimally solve virtually any machining task.
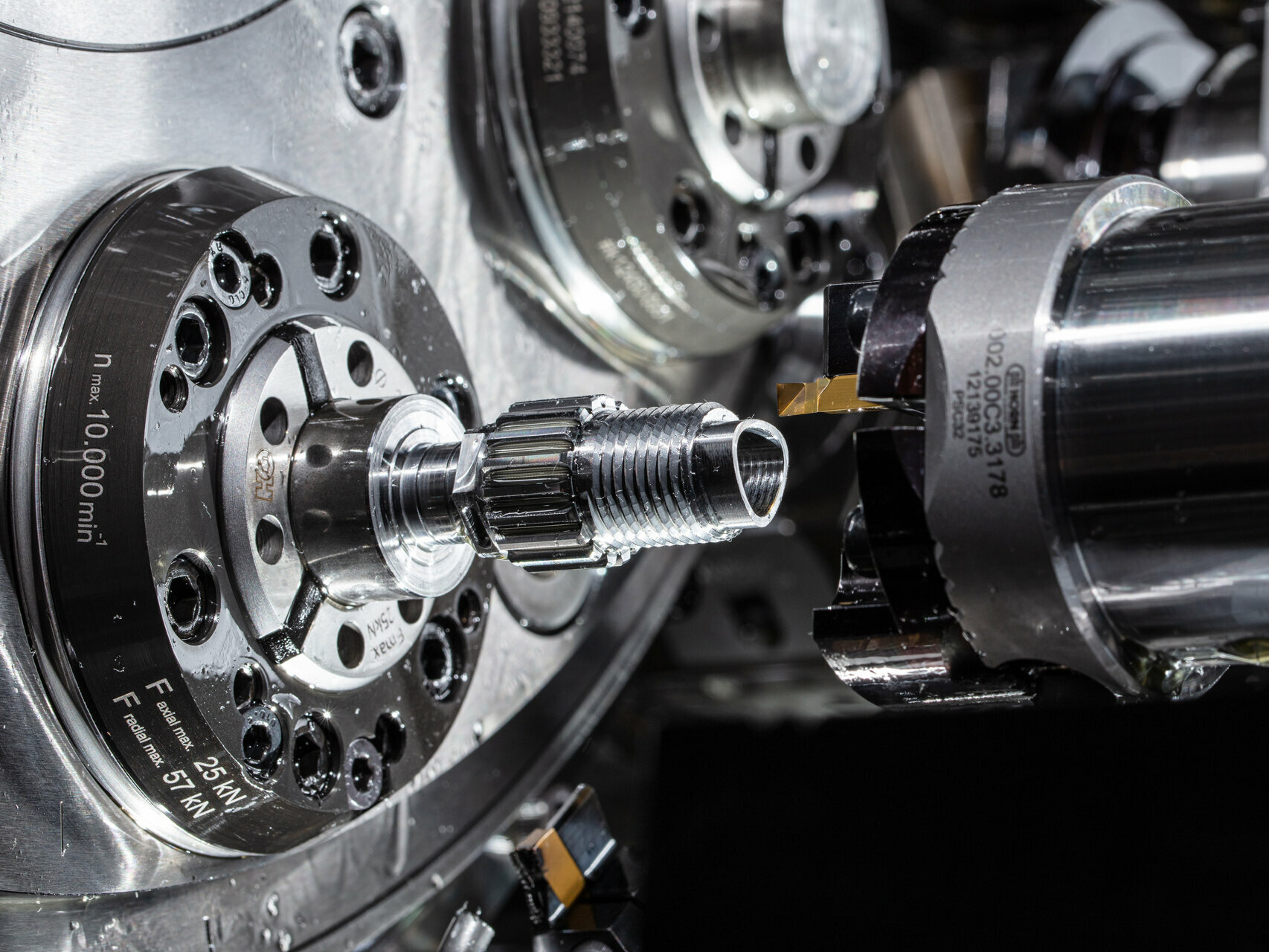
Polygon turning
In polygon turning, the challenge is synchronisation of the lathe axes. Synchronisation is playing an increasingly important role in machining. Modern turning machine concepts from INDEX allow such complex processes. Using axial feed, HORN tools offer the possibility of producing non-round contours on lathes. This process facilitates the production of polygon shapes, for example. The axes of the workpiece and tool are offset from each other and maintained at a specific speed ratio. The process and associated tools are suitable for both external and internal machining. The axis offset, the speed ratio of the workpiece to the tool and the diameter of the cutter define the dimensions of the contour. A tool system for polygon turning is individually adapted to the workpiece contour to be produced.
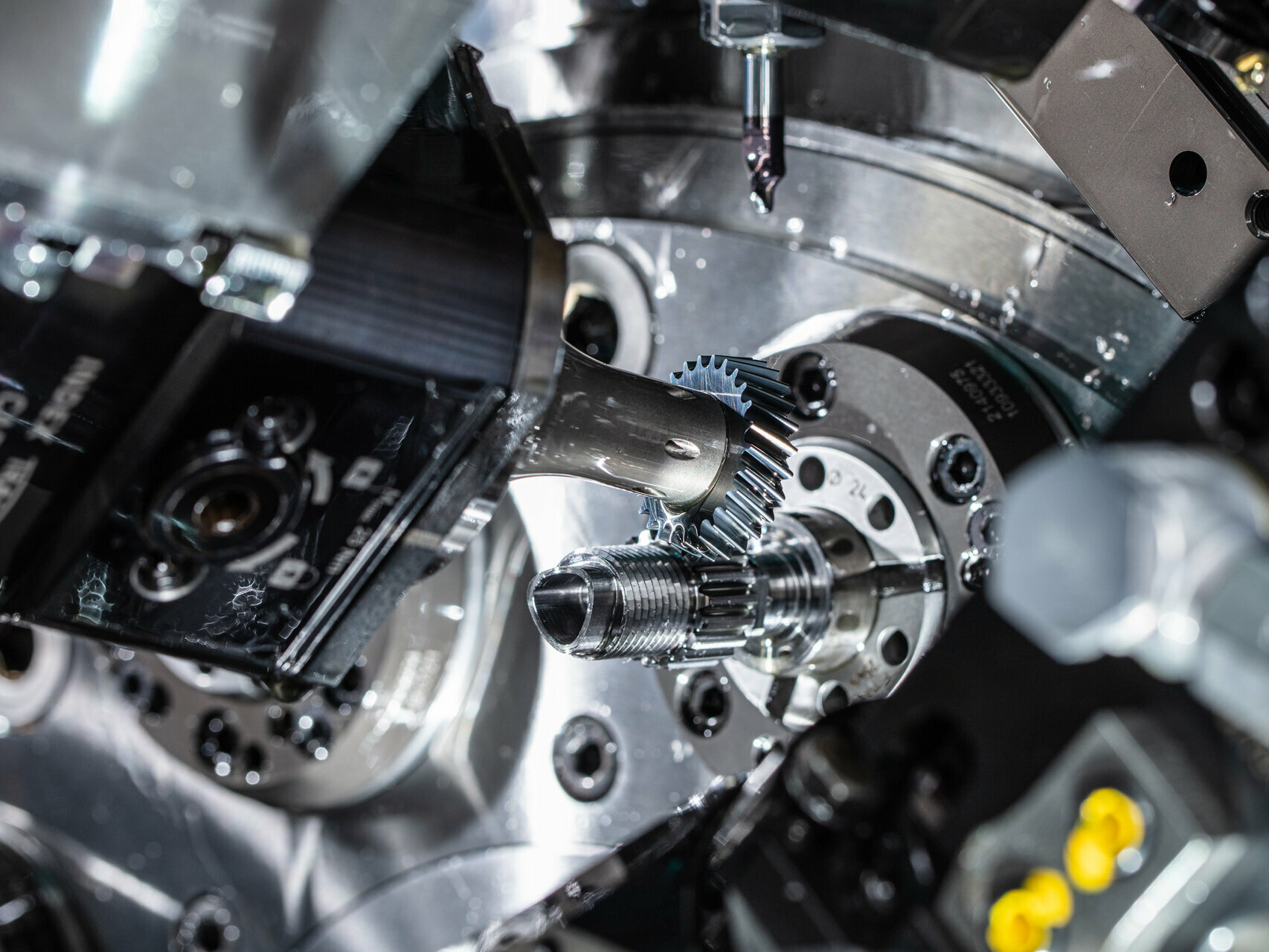
Skiving
Modern turning/milling centres and multi-spindle automatic lathes from INDEX with coupled and synchronised spindles and process-optimised software enable gear skiving. The associated HORN tool system includes tools for the highly productive production of internal gears, splines and other internal profiles as well as external gears with interfering edges. The main advantages of skiving in these applications are significantly shorter process times compared to gear broaching, the ability to use optimised turning/milling centres, turning and gear cutting in one clamping and the elimination of undercuts at the end of the gear teeth. In addition, skiving offers more productive and cost-effective production compared to gear shaping and broaching and a cycle time that is four to five times shorter compared to slotting. It also allows the possibility of hard machining of solid gear blanks. The skiving tools are designed for machining medium to large batches. Each tool is individually adapted to the application and the material to be machined, with the different tool interfaces being based on the number of teeth and the module. For the production of defined chamfers for deburring the gears, the technology is available together with the associated production process. The prerequisite for this manufacturing process is a turning/milling centre with coupled axes.
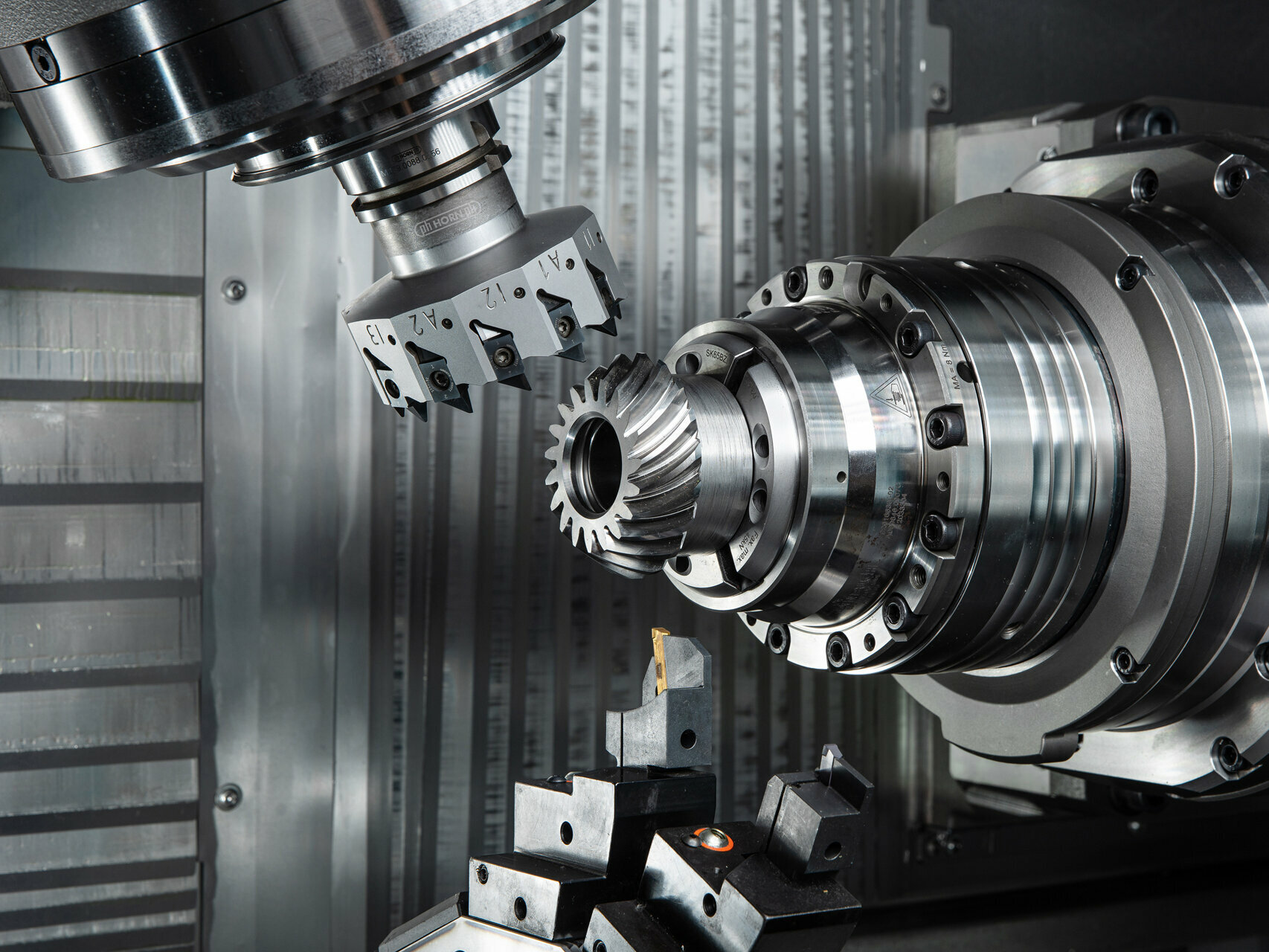
Bevel gear cutting
In cooperation with INDEX, HORN offers a solution for milling spiral bevel gears. Thanks to the use of special milling tools and the appropriate machining cycle, even small series can be milled economically. With the new tool system for milling bevel gears, complete machining on turning/milling centres is possible. The user no longer needs special machines to manufacture these gears, as INDEX has developed a bespoke cycle for this type of machining. This allows all functional surfaces to be produced together with the gear teeth in one clamping. It enables high component precision, short throughput times, high process efficiency and fast machining times due to controlled machine cycles. By using a turning/milling centre from INDEX, components with spiral bevel gears can be produced efficiently both in small quantities as well as in large batch sizes. This also makes the process attractive for medium-sized and small companies that previously bought in gears or had them manufactured externally.
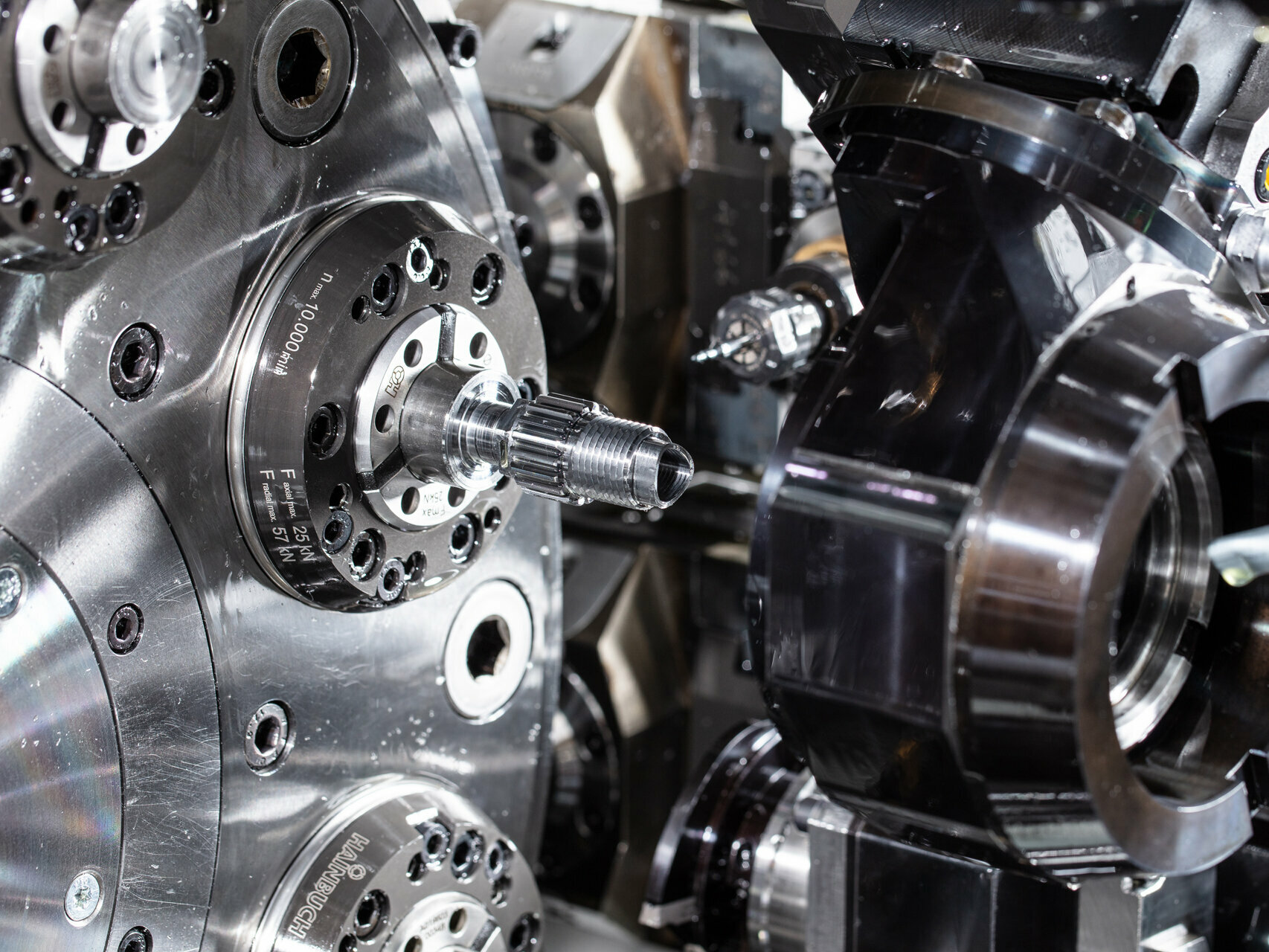
High-speed whirling
INDEX and HORN are showing another new process with high-speed (HS) whirling. It offers a substantial increase in productivity through turning and whirling in one set-up. In this process, the speed is so high that a turning process can take place simultaneously with whirling if required. The turning tool positioned in front of the whirling tool reduces the volume of material that would otherwise have to be removed by the whirling tool. This enables longer tool life and leads to higher surface quality. The whirling heads used are similar to conventional varieties. Only the inserts differ in geometry. The production of single and multi-start threads is possible with only one set of inserts. Thread whirling is mostly used in the production of bone screws and worm gears. The whirling head rotates at a high speed over the workpiece, which also rotates quickly. The whirling head is set at a special approach angle. Due to the axial feed, the whirling tool mills the thread. As the demands on the quality of the threads are high, special attention is paid to the precision and surface quality of the whirling tools.
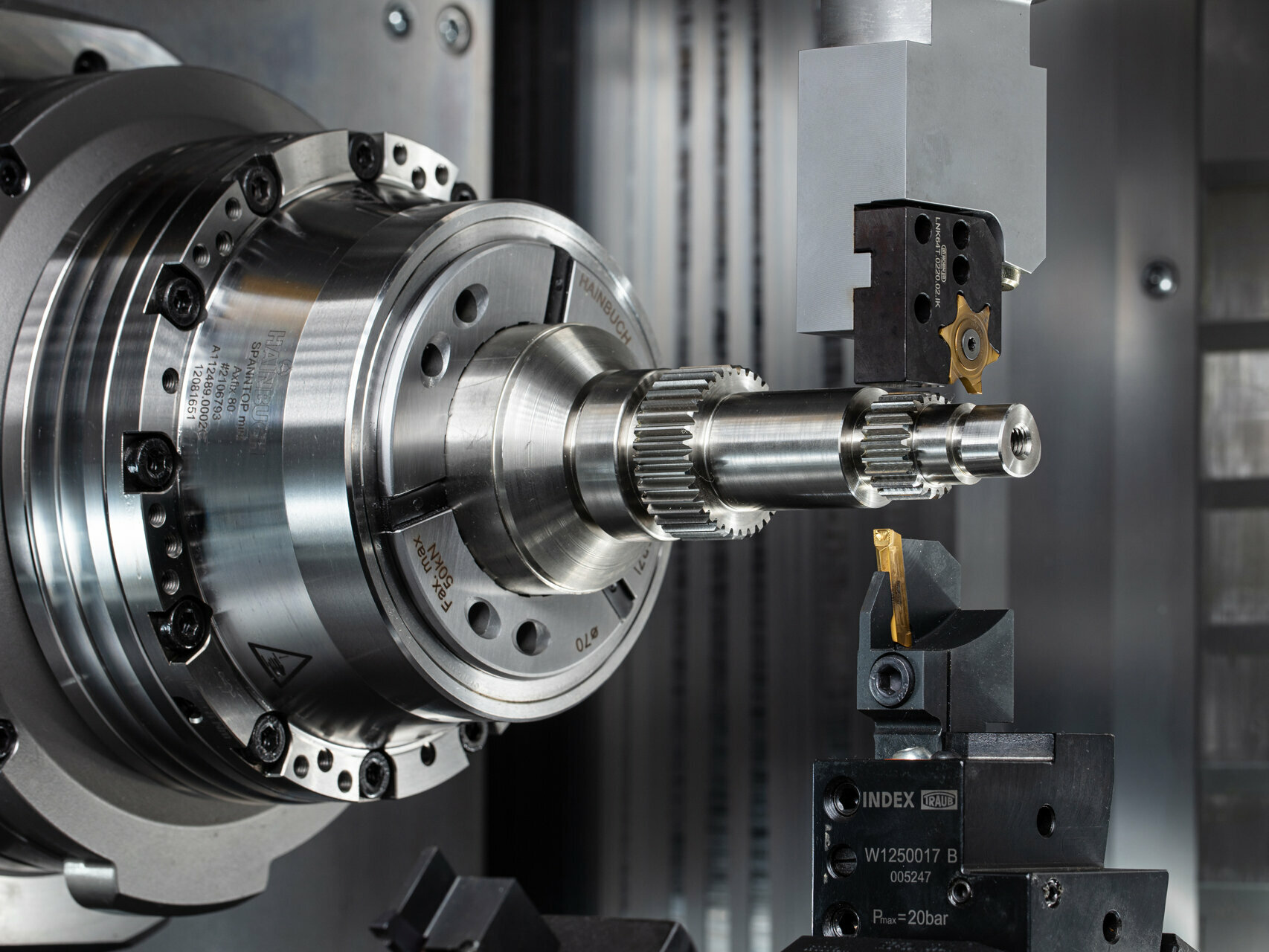
Grooving
Basically, the grooving process involves a narrow insert that penetrates the workpiece in a radial or axial direction. The art of grooving is, among other things, controlling the chip flow. Bent chips, chip jams or long, stringy swarf must be avoided, as they have a negative impact on process reliability and can lead to tool breakage and marking of shoulders. Depending on the material to be machined and the type of process, Horn has developed different chipbreaker geometries that ensure reliable chip taper, chip control and chip breakage. Another important point for an economical grooving process is sufficient coolant supply. Where in the past cooling was carried out externally using classic flood coolant, today modern tool carriers mostly have an internal coolant supply. This ensures effective cooling of the shear zone between the tool cutting edge and the workpiece. HORN and INDEX offer an ideal technology platform through the combination of precision tool and machine.