Whirling for excellent sound quality
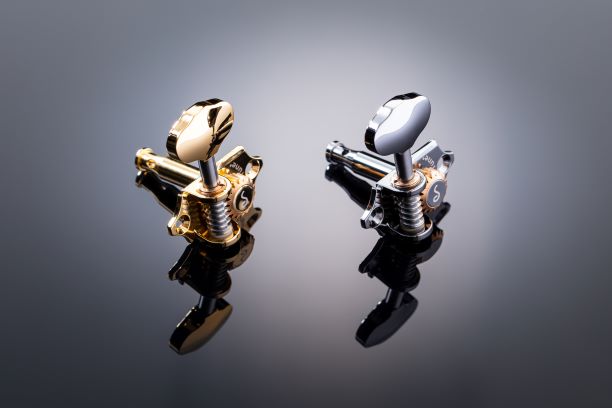
Music makes people happy one moment and can bring them to tears the next. It can help drive people to peak performance in sports, or make them anxious. But one thing that music never does is leave you cold. And the guitar evokes more emotion than virtually any other instrument. Whether around a camp fire or at a rock concert in a stadium, the way guitars work is always the same. Schaller GmbH, based near Nuremberg, has been dealing with the functioning of this plucked instrument for over 75 years. During this time, the company has become the world market leader in guitar parts. With modern machinery, the team led by plant manager Dominik Weininger turns and mills the precise components required to produce excellent sound quality. It also relies on the internally cooled whirling system from Tübingen-based Paul Horn GmbH.
A central part of the machine head is the adjusting screw with the worm thread. Department head of CNC turning and milling Nicole Gawatsch saw potential for improvement in this thread. “We previously milled the worm thread with a side milling cutter. The machining time required was too long for us and we often had to take the part and re-clamp it by hand”, Gawatsch explains. “We became aware of HORN’s internally cooled jet whirling at AMB 2018 and immediately contacted our HORN sales representative”, continues plant manager Weininger. Initial discussions with HORN about the new whirling system and the start of the project quickly followed.
“The whirling unit has been running 24/7 in the machine for over a year. We are very satisfied with the tool system”, says plant manage Weininger. The successful change in the process is also reflected in the processing time. Previously, Gawatsch needed about a minute to mill the worm thread. Conventional whirling takes 40 seconds. “With internally cooled whirling, we have halved the machining time to just 20 seconds per component. Given the incredibly high number of components we process each year, this is an enormous saving”, Gawatsch explains. In addition to the reduced machining time, the surface quality of the finished components is also improved significantly. Moreover, the service life of the indexable inserts has increased many times over.