Mükemmel Müzik Sesi için Whirling
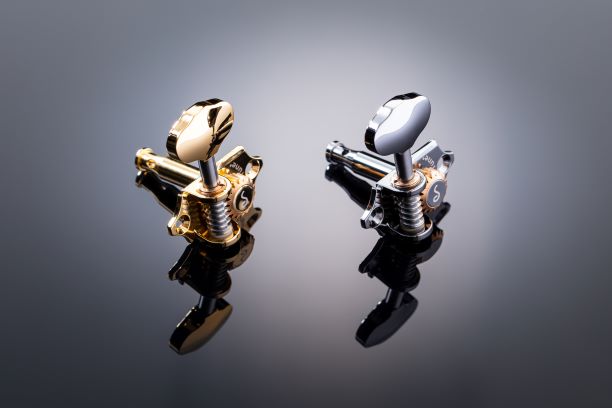
Müzik insanları bir an mutlu ederken bir an sonra gözyaşlarına boğabilir. İnsanların sporda performansı zirveye çıkarmasına veya endişelerini almaya yardımcı olabilir. Ama müziğin asla yapmadığı bir şey vardır, sizi asla duygusuz bırakmaz. Ve gitar neredeyse tüm diğer enstrümanlardan daha fazla duygu uyandırır. İster bir kamp ateşinin etrafında, ister bir stadyumdaki rock konserinde, gitarların çalışma şekli her zaman aynıdır. Nürnberg yakınlarında bulunan Schaller GmbH, 75 yılı aşkın bir süredir bu aletin işleyişiyle uğraşıyor. Bu süre zarfında şirket, gitar parçalarında dünya pazar lideri haline geldi. Tesis müdürü Dominik Weininger liderliğindeki ekip, modern makinelerle, mükemmel ses kalitesi elde etmek için gereken hassas parçaları tornalar ve frezeler. Aynı zamanda Tübingen merkezli Paul Horn GmbH'nin içten soğutmalı Whirling sistemine de dayanmaktadır.
A central part of the machine head is the adjusting screw with the worm thread. Department head of CNC turning and milling Nicole Gawatsch saw potential for improvement in this thread. “We previously milled the worm thread with a side milling cutter. The machining time required was too long for us and we often had to take the part and re-clamp it by hand”, Gawatsch explains. “We became aware of HORN’s internally cooled jet whirling at AMB 2018 and immediately contacted our HORN sales representative”, continues plant manager Weininger. Initial discussions with HORN about the new whirling system and the start of the project quickly followed.
“The whirling unit has been running 24/7 in the machine for over a year. We are very satisfied with the tool system”, says plant manage Weininger. The successful change in the process is also reflected in the processing time. Previously, Gawatsch needed about a minute to mill the worm thread. Conventional whirling takes 40 seconds. “With internally cooled whirling, we have halved the machining time to just 20 seconds per component. Given the incredibly high number of components we process each year, this is an enormous saving”, Gawatsch explains. In addition to the reduced machining time, the surface quality of the finished components is also improved significantly. Moreover, the service life of the indexable inserts has increased many times over.