Mastering processes: polygon turning
Polygon turning is not often seen on a lathe, as the process and function are not well understood. The challenge is the synchronisation of the axes. Synchronisation plays an increasingly important role in machining and modern machine concepts allow such complex processes. Using axial feed, tools from Paul Horn GmbH offer the possibility of producing non-round contours on lathes. This process facilitates the production of polygonal shapes, for example. The axes of the workpiece and the tool are offset from each other and are rotated at a specific speed ratio. The process and the associated tools are suitable for both external and internal machining. The axis offset, the rotational speed ratio of the workpiece to the tool and the cutting edge diameter define the dimension of the contour. Philipp Dahlhaus, Head of Product Management at Horn commented, "A tool system for polygon turning is individually adapted to the contour of the workpiece to be produced. Horn has a design department for creating these tools. There are specific methods by which such tools can be calculated."
A practical example
The customer's component has an internal polygon with three corners, similar to a polygonal shank adapter, only cylindrical. The application runs on a multi-spindle automatic lathe. The material is 42CrMo4 (1.7225). The aim was to produce the polygon in the shortest possible cycle time. The problem in this application was the small diameter-to-length ratio of the tool. Dahlhaus explained, "Originally, a milling operation was planned for this application. This resulted in the problem that the milling cutter was deflected, which would have necessitated an additional finishing process, but that was not possible due to time constraints. We therefore attempted to produce the profile by polygon turning.". The component is pre-bored,the component and tool rotations are synchronised and feed is in the Z-axis only, there being no X-axis movement. The tool is adjusted by hand using a presetter. The infeed takes place in one operation, as the tool is designed so that the full depth of cut (ap) is achieved in one pass. Speaking of what was achieved at the customer, Dahlhaus said, "There was a time saving of ten seconds compared to the milling process. The customer considered this result a great success. Process reliability was excellent and there was no deflection of the tool. The polygon turning solution impressed the customer."
Process thinking
Every machining operation is a process: grooving, parting off, slot milling or face milling. Processes that are an everyday reality for machinists are stored as cycles in every machine control. Horn offers a wide range of tools for these applications within its tool portfolio. In addition, more specialised machining processes such as hobbing, bevel gear milling, thread whirling, high-polish milling and turning or speed-forming require a high level of know-how in tool technology and processes. This includes, for example, the design of the tool cutting edges when whirling the multi-start thread of a bone screw or skiving the tooth profile of gears.
According to Dahlhaus, Horn also demonstrates with the polygon turning process that the company is not only there to support its users as a pure precision tool manufacturer. With its know-how in tool manufacturing and extensive process knowledge, the Tübingen-based specialist also sees itself as a problem solver for special machining solutions. Dahlhaus concluded, "Only those who have mastered the machining process can get the maximum performance out of the tool. But if you don't master the tool, you won't achieve economical results even with the best process knowledge. Our technicians combine know-how in the manufacture of precision tools as well as the productive machining process.
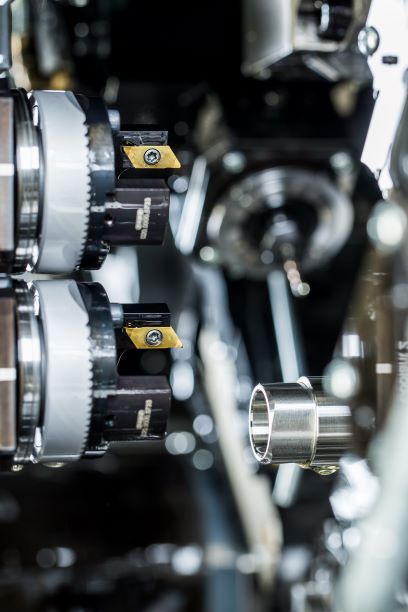