Precision is a passion
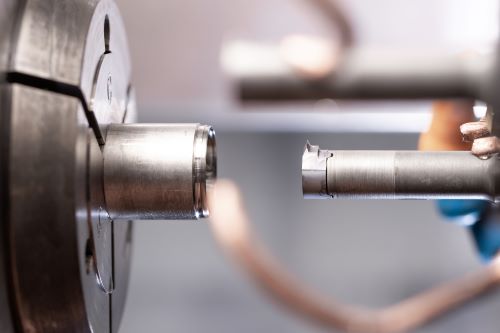
Shortness of breath, dizziness and a feeling of pressure in the chest – if the pockets, or leaflets of the aortic valve no longer open sufficiently for the blood to flow, it is known as aortic valve stenosis. This heart defect can only be treated with an artificial aortic valve. The Italian company Corcym from Saluggia uses its extensive expertise to produce the implants, helping people to improve their quality of life and saving lives. Tolerances in the micron range and materials that are difficult to machine are the order of the day for the production of these small marvels. In order to machine them productively, the company relies on tools from HORN and technical advice from Febametal.
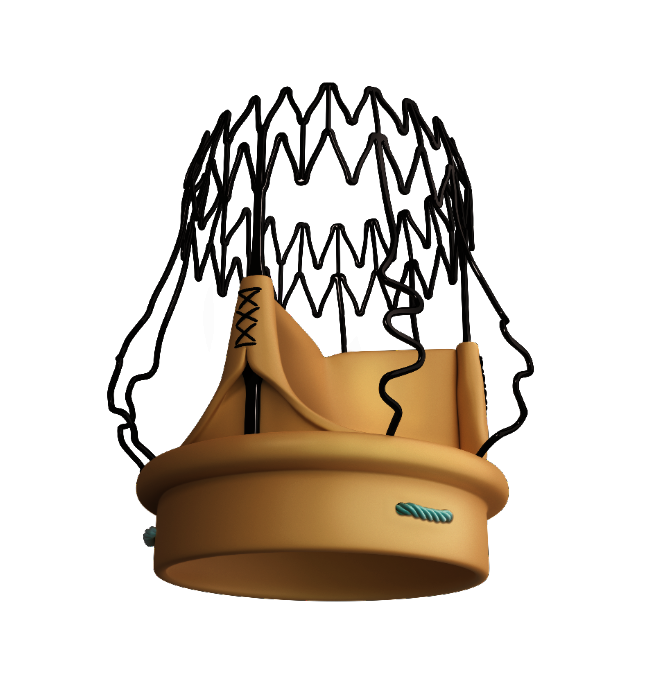
One of the most common heart defects is aortic valve stenosis. This is a narrowing of the aortic valve. As a result, the flow of blood from the left ventricle into the aorta is impaired. If the narrowing is severe, symptoms such as shortness of breath, pressure, dizziness and loss of consciousness can occur. The disease is usually caused by wear and tear processes such as calcification and hardening of the tissue. Aortic valve stenosis usually occurs only in old age. The narrowing cannot be treated with medication. Depending on the clinical picture, an implant may have to replace the valve. The patient's individual circumstances determine whether the valve is inserted minimally invasively through the femoral artery or conventionally through an opening in the sternum.
Flaps made from bovine tissue
The respective implants differ in terms of structure and material. For minimally invasive surgery (TAVI procedure), the implant must be movable and expandable so that the surgeon can manoeuvre it through the blood vessels into the heart. Due to the short shelf life of 10 to 15 years, biological aortic valves are given to elderly people or patients who are unable to undergo open heart surgery for health reasons. The construction of a biological implant is complex. The artificial valve made of a biological material is sewn by hand around an expandable wire mesh. At Corcym, this material is obtained from bovine tissue. The tissue, from specially bred cattle, is processed in such a way that it no longer contains any DNA or living cells so the body will not reject it.
The other option is the use of a mechanical aortic valve prosthesis. Mechanical valves are characterised by their lifelong durability, meaning that a repeat operation is unlikely. The implant is inserted into an open heart. The patient is connected to a heart-lung machine during the operation. The design is simple. Two movable flaps are mounted in a plastic ring that will open and close with the blood flow. A synthetic fabric is stretched around the ring. The surgeon sutures this tissue to the aorta during insertion. Even if the structure and function are simple, the production of the mechanical aortic valve is complex.
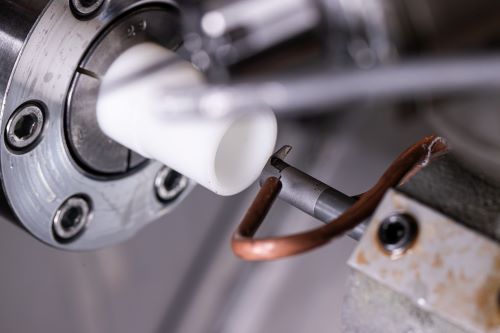
Stringent requirements
"The production of the mechanical components is very complex. We check every manufactured component under a microscope at 20x magnification," explains process engineer Davide Ricchiari. The components must not have any scratches or burrs. Any imperfection, no matter how small, could lead to a stress fracture or harbour germs. Rough surfaces could also lead to calcification of the components, which would impair function. "To ensure perfect function, all components are manufactured to tolerances of just a few microns. Furthermore, the tolerances are also necessary for the certification of the implant. A human life depends on these components in later use, which is why we work here with the utmost care," says Ricchiari.
The outer ring of the mechanical implant is made from a special plastic. The micron tolerances for the internal turning of plastics require a great deal of expertise. The focus is on roundness and diameter tolerance. If these are not met, the two inserted valves will not close tightly. As a result, blood could flow back into the heart due to the patient's blood pressure. Corcym uses PCD-tipped inserts in HORN's Mini range to bore the rings. "The material is highly abrasive. A sharp carbide cutting edge is rounded after just a few components," explains Febametal application engineer Andrea Panichi. This was precisely the reason for switching to the diamond PCD grade. Before switching to the new special material, the rings were made from a less abrasive plastic. "The production of the rings was very time-consuming. After roughing, we had to heat treat the parts to relieve the stresses in the material. Otherwise, we would not have been able to maintain the tight roundness tolerances during finishing," says Ricchiari. Switching to the PCD grade achieved the same performance as carbide when machining the previous material. Heat treatment before finishing is no longer necessary with the new plastic, but the material is not easy to machine. "A sharp insert is very important," says Panichi. Excessive cutting pressure can lead to deformation of the thin-walled ring and thus to ovality.
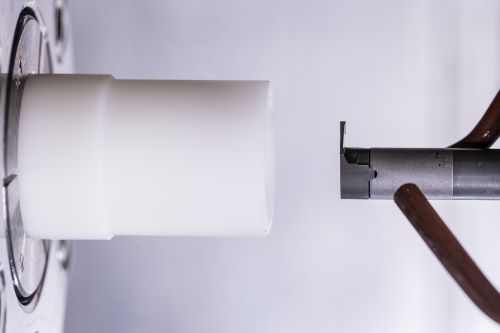
Titanium lock ring
Another important component of the mechanical aortic valve is the lock ring made of a titanium alloy. The ring tensions the tissue layer, which is sewn to the aorta, to the plastic ring. Put simply, it functions like a locking ring used in mechanical engineering. If it fails, the ring with plastic flaps could come loose and travel up the aorta with the blood flow. Great care is also required when manufacturing the ring. "The rings must be perfectly round on the flanks. Burrs or sharp transitions could damage the synthetic fabric when it is tensioned. The rings are subject to a 100 per cent inspection under a microscope," explains Ricchiari.
A Mini 108 insert is also used for boring. It is precision-ground with a special profile that also allows it to be used for parting off the ring. During the production process, the machine pre-turns the rings on the outside and inside. Several rings are turned, which are connected to each other by a narrow web. The rings are then parted off.
Extensive portfolio
The face-clamped inserts of the Mini type are one of HORN's core products. The tool system is mainly suitable for turning applications. The precision tools have proven themselves in particular for internal turning and grooving. With the vibration-damped carbide tool holders, the inserts produce good surface finishes even with long overhangs and ensure highly reliable processes. The Mini system's extensive portfolio offers inserts in various sizes for different internal diameters, geometries and substrates as well as CBN or diamond coatings.
Corcym has been relying on HORN tool solutions for over 15 years. In addition to the Mini systems, numerous Supermini types are also used for boring. "We regularly test various tool systems from different manufacturers. So far, no others have delivered anywhere near as convincing a performance as the HORN products. Furthermore, Febametal's technical advice is always a great support for us," says Ricchiari.
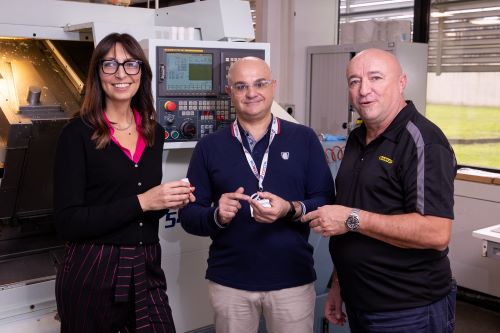
Corcym
With a history dating back more than 50 years, Corcym is an independent, global medical industry company focused on alleviating structural heart disease. Corcym's vision is to become the leading company for cardiac surgeons and their patients by providing the best solutions to combat structural heart disease, for which the company has a broad portfolio of approved and patented products. Corcym has two FDA- and EMA-certified manufacturing and R&D sites in Italy and Canada.