Wonders of technology – Gear cutting
No cars, watches or machines could function without gears. The technical world and our everyday lives would be unthinkable without them. The production of precise gears can be a challenge for the manufacturer. The choice of tooling solution for the production of gears depends on various factors: Module sizes, batch sizes and the available machine technology are the main factors that determine the manufacturing technology to be selected. In particular, the newer machine tools with coupled and synchronised axes today offer possibilities for gear manufacturing that were previously reserved for special machines.
A distinction is made between gears and shafts with internal or external teeth. Gears can be spur, straight, helical or herringbone, as well as straight-toothed or spiral bevel, helical gears in which the two axes do necessarily have a common point of intersection, as well as similar hypoid gears. A gear can also be a worm in a worm gear. A special form is, for example, the toothed rack. Depending on the position of the axes in relation to each other, the gears are subdivided into roller gears and screw gears.
The most common tooth form is the involute. Involute gears are equally suitable for transmission ratios from fast to slow and vice versa, and for clockwise and counter-clockwise rotation. They have relatively low backlash and are simple and inexpensive to manufacture. The second important type of gear is cycloidal. Its advantages are low friction in the transmission from slow to fast and larger feasible transmission ratios. However, this type of tooth is more demanding in terms of design and production. So-called pinion gears no longer play a major role (except for the special form of chain drive as found in bicycle and motorbike drives).
The measure of the size of the teeth in a gear is the module. It is defined as the quotient of the gear pitch p (the distance between two adjacent teeth) and the constant Pi. Variables of the teeth such as tip and root height, root radius and tip chamfer are specified with the module. In order to be able to use standardised tools, DIN 780 standard is used. In the preferred series I they range from module 0.05 to module 60 and in the preferred series II from module 0.055 to module 70. In the Imperialsystem of measurement, the "diametral pitch" is used instead of the module.
Machining processes with a geometrically defined cutting edge are hobbing, profile milling, planing, shaping, broaching, skiving, profile broaching, 5-axis free-form milling and shaving. Machining processes with indeterminate cutting edges are gear or profile grinding, honing, lapping, eroding and etching. For large series machining of gears in mechanical and automotive engineering, one relies primarily on machine tools with special kinematics and elaborately designed tools, such as gear hobbing machines. These expensive investments usually only pay for themselves when producing large series. Demanding and precise tooth contours can be machined on common CNC turning centres and CNC machining centres with tools adapted to the application.
HORN's product portfolio includes a wide range of tools for the production of different gear tooth geometries from module 0.5 to module 30. Whether teeth on spur gears, shaft-hub connections, worms, bevel gears, pinions or on customised shapes, all these tooth profiles can be produced economically today with tools for milling, grooving and other processes. Further proof of competence in gear cutting is provided by the gear skiving product range. The process has been known for over 100 years. However, it has only found wider application since machining centres and universal turning machines with fully synchronised spindles and process-optimised software have made it possible to use this highly complex technology.
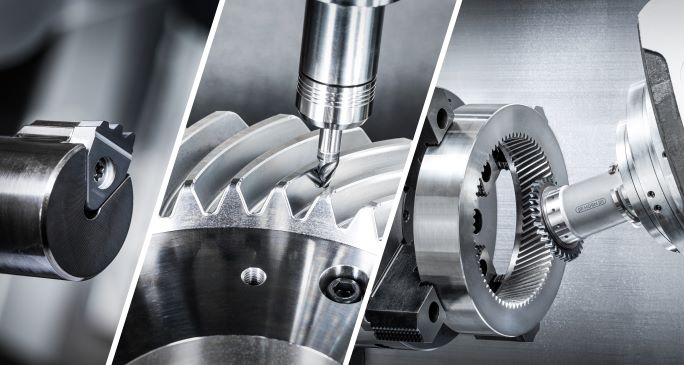