Wunderwerke der Technik – Verzahnungen
Keine Autos, keine Uhren und keine Maschinen funktionieren ohne Verzahnungen. Die technische Welt sowie unser gewohnter Alltag wären ohne Zahnräder nicht denkbar. Die Herstellung von präzisen Verzahnungen kann für den Anwender eine Herausforderung darstellen. Welche Werkzeuglösung bei der Fertigung von Verzahnungen zum Einsatz kommt, hängt von verschiedenen Faktoren ab: Modulgröße, Losgrößen und die vorhandene Maschinentechnologie sind die wesentlichen Faktoren, die über die zu wählende Fertigungstechnologie entscheiden. Insbesondere die neueren Werkzeugmaschinen mit gekoppelten und synchronisierten Achsen bieten heute Möglichkeiten zur Verzahnungsherstellung, die früher Spezialmaschinen vorbehalten waren.
Man unterscheidet innen- und außenverzahnte Zahnräder sowie Zahnwellen. Zahnräder kommen vor als Stirnräder, geradeverzahnt, schräg- oder pfeilverzahnt, als gerade- oder bogenverzahnte Kegelräder, Schraubenräder, bei denen die beiden Achsen keinen gemeinsamen Schnittpunkt haben müssen, ebenso wie die ähnlichen Hypoidräder. Ein Zahnrad kann aber auch eine Schnecke sein in einem Schneckengetriebe. Eine Sonderform ist zum Beispiel die Zahnstange. Die Zahnradgetriebe unterteilt man, je nach Lage der Achsen zueinander, in Wälzgetriebe oder Schraubgetriebe.
Die am häufigsten verwendete Zahnform ist die Evolvente. Evolventenverzahnungen sind gleichermaßen geeignet für Übersetzungsverhältnisse von schnell zu langsam und umgekehrt, für rechts- und linksdrehend. Sie sind relativ spielarm und einfach sowie kostengünstig herzustellen. Die zweite wichtige Verzahnungsform ist die Zykloidenverzahnung. Ihre Vorteile sind geringe Reibung bei der Übersetzung vom Langsamen zum Schnellen und die größeren möglichen Übersetzungsverhältnisse. Konstruktiv und fertigungstechnisch stellt diese Zahnform allerdings höhere Ansprüche. Daneben spielen sogenannte Triebstockverzahnungen (außer bei der Sonderform Kettenantrieb wie bei Fahrrad- und Motorradantrieben) keine größere Rolle mehr in der Technik.
Das Maß für die Größe der Zähne bei Zahnrädern ist das Modul. Es ist definiert als Quotient aus der Zahnradteilung p (dem Abstand zweier benachbarter Zähne) und der Kreiszahl Pi. Bestimmungsgrößen der Zähne wie Kopf- und Fußhöhe, Fußrundungsradius und Kopfkantenbruch werden als Produkte mit dem Modul angegeben. Um standardisierte Werkzeuge verwenden zu können, sind in der DIN 780 Vorzugsreihen definiert. Sie reichen bei der Vorzugsreihe I von Modul 0,05 bis Modul 60 und in der Vorzugsreihe II von Modul 0,055 bis Modul 70. Im angloamerikanischen Maßsystem wird statt des Moduls der „Diametral Pitch“ verwendet.
Bearbeitungsverfahren mit geometrisch bestimmter Schneide sind Abwälzfräsen, Profilfräsen, Wälzhobeln, Wälzstoßen, Stoßen, Wälzschälen, Profilräumen, 5-Achs-Freiformfräsen oder Schaben. Bearbeitungsverfahren mit unbestimmter Schneide sind Wälz- oder Profilschleifen, Honen, Läppen, Erodieren oder Ätzen. Bei der Großserienbearbeitung von Zahnrädern im Maschinen- und Automobilbau setzt man vor allem auf Bearbeitungsmaschinen mit spezieller Kinematik und aufwendig konstruierten Werkzeugen, wie zum Beispiel Wälzfräser. Diese teuren Investitionen rechnen sich in der Regel nur bei großen Serien. Auf gängigen CNC-Drehzentren und CNC-Bearbeitungszentren und mit auf den Anwendungsfall angepassten Werkzeugen können wirtschaftlich anspruchsvolle und präzise Zahnkonturen bearbeitet werden.
Das Produktportfolio von HORN umfasst ein breites Werkzeugprogramm zur Herstellung von unterschiedlichen Verzahnungsgeometrien ab Modul 0,5 bis Modul 30. Ob Verzahnungen an Stirnrädern, Welle-Nabe-Verbindungen, Schneckenwellen, Kegelrädern, Ritzeln oder an kundenspezifischen Profilen, alle diese Zahnprofile lassen sich mit den Werkzeugen zum Fräsen, Nutstoßen und anderen Prozessen heutzutage wirtschaftlich herstellen. Einen weiteren Beweis der Kompetenz beim Verzahnen bietet das Produktprogramm Wälzschälen. Das Verfahren ist seit über 100 Jahren bekannt. Eine breitere Anwendung findet es aber erst, seit Bearbeitungszentren und Universalmaschinen mit voll synchronisierten Spindeln und verfahrensoptimierter Software die Anwendung dieser hochkomplexen Technologie ermöglichen.
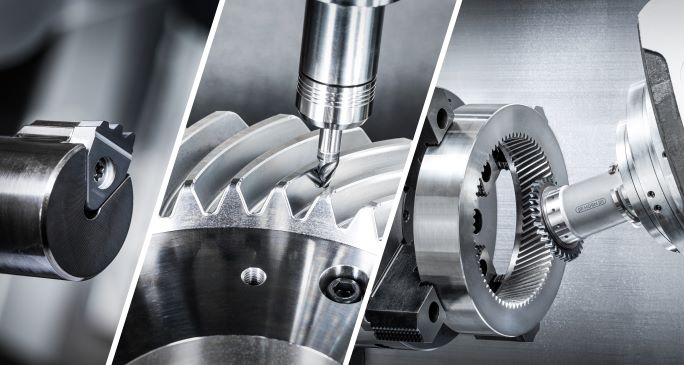