Mastering processes: High-performance reaming
Tight bore tolerances, high surface quality and almost perfect cylindricity. Boring with reaming tools is often the last machining step in the production of precise components. In addition to the features mentioned, other properties play an important role in the production of close tolerance bores. Reaming tools are usually used for this purpose. In addition to the well-known HSS reamers, special high-performance reaming systems are increasingly proving their worth in modern production. With the DR reaming system, Paul Horn GmbH offers its own product portfolio for the economical finishing of bores.
As with other tool systems, high-performance reaming systems are also subject to demanding requirements. In addition to high process reliability, long tool life and low tool costs, modern reaming tools must fulfil further criteria. These include, among other things, the modularity of the tools. While machining with an HSS reamer is partially limited in this respect, modern reaming systems can be improved by replaceable heads with carbide inserts, modular tool lengths and various adjustment options. These include, for example, µ-accurate adjustment of concentricity and runout. Precise concentricity of the reaming inserts is the path to success. In practice, this should be within 5 µm.
Chip control
In addition to the precise grinding of the carbide insert, the appropriate tool geometry for the machining operation also plays an important role in economical reaming. Therefore, two insert orientations or side rake angles are used for reliable chip removal. Straight-insert reaming cutters are suitable for machining blind holes. Chip flow is in the opposite direction to the machining direction. Left-hand helical inserts are designed for reaming through holes only. In this case, the direction of chip flow and machining is the same.
Controlling chip breaking is an important aspect of successful boring. In deep bores, with low coolant pressure or dry machining, helical or ribbon swarf can occur. As with drilling with twist drills, the chips can be broken by briefly lifting the reamer. It is important to program as few interruptions as possible, but as many as necessary, as retractions can reduce the service life of the cutting edges. The lifting of the tool is hardly noticeable in the appearance of the machined surface.
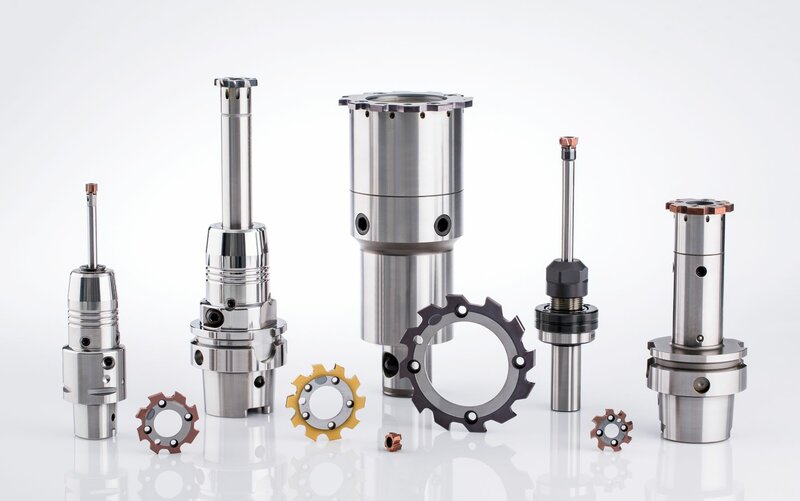