Chipping problems solved
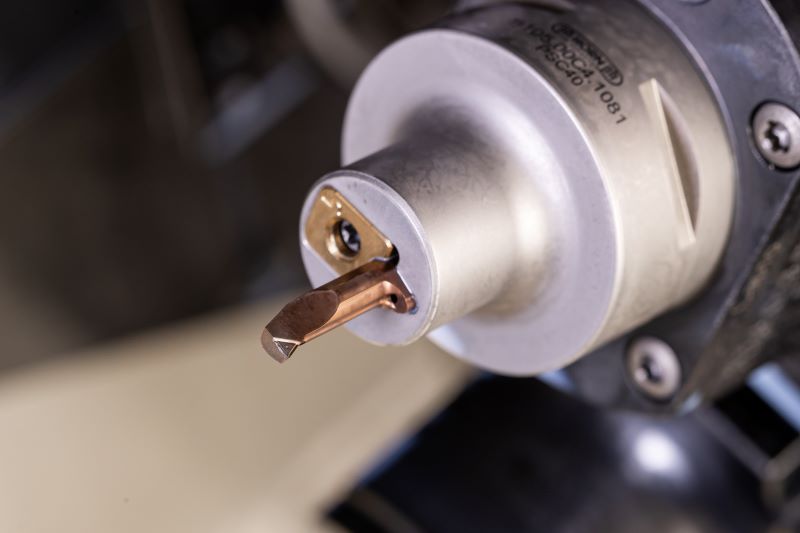
"Our machining problems were solved after the first component," says Hakan Oda, talking about the new HORN Supermini with sintered geometry. Oda and his colleagues are responsible for tooling in the machining department at Endress+Hauser. The metrology company was one of the users that was able to test the new Supermini in field trials. The field tests were the first milestones in HORN’s progress. "We could hardly wait for the market launch, as the tools have brought us many advantages," says Oda.
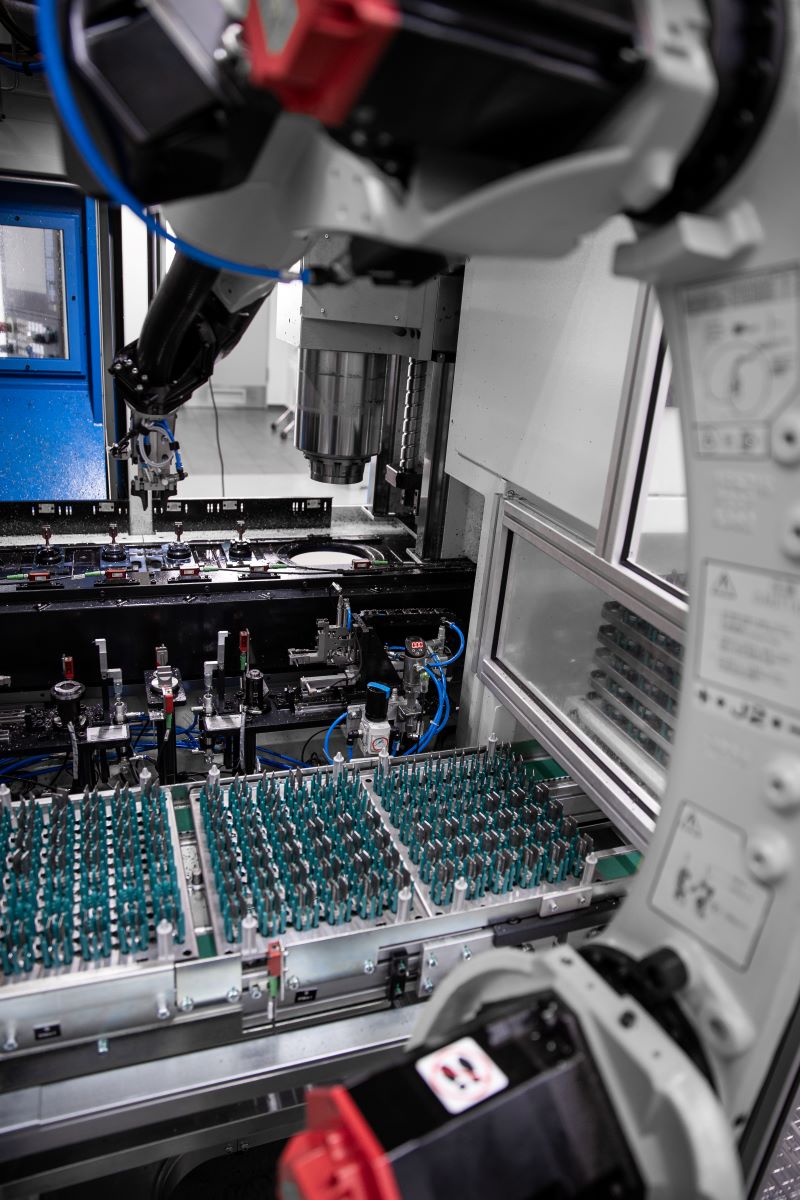
HORN provided the Endress+Hauser team with six Superminis with sintered chip breaking geometry for the tests. Customers are selected for field trials according to certain preconditions. "We know our users and their machining problems. The choice quickly fell to Endress+Hauser," says HORN application engineer Stefan Minder. In the metalcutting processes at Endress+Hauser, the team mainly machines materials such as 1.4404 (X2CrNiMo17-12-2), 1.4435 (X2CrNiMo18-14-3) and Hastelloy (2.4819, NiMo16Cr15W).
Chipping problems
The materials to be machined have numerous advantages for use in metrology. They include, for example, corrosion resistance or acid resistance. For economical machining, however, the materials require a great deal of expertise on the part of the user. This applies in particular to the series production of large quantities. Especially when turning smaller diameters, the problem arises of long, tangled chips that wrap around the tool like a bird's nest. This significantly limits process reliability and, in the worst case, leads to tool breakage. At Endress+Hauser, a stop had to be programmed after every fifth part in the automated production of M-forks to manually free the tangled swarf from the tool. The swarf also impaired in-process measurement and the gripping actions of the robot in the machining cell.
A Supermini without chip breaking geometry was previously used. "The problem of long swarf can only be solved with chip breaking geometry. Regardless of the quality of the tool, this problem always exists," says Minder. The Endress+Hauser team was already impressed after the first trial with the new Supermini with sintered geometry. "Our problems were literally solved at the push of a button. The swarf from internal turning was no longer tangled, but short, curled chips," says Oda. The team kept the cutting parameters the same as with the previous tool. Minder and the Endress+Hauser team tested the tools on various machines and components for a total of four weeks. The tool showed its potential in all processes. "We would have liked to order more tools straight away, but we had to wait for the official market launch," says Oda.
Long development time
"We have been working intensively on the develop ment of the new Superminis for over four years," said HORN CEO Matthias Rommel at the press conference held to launch the new tool in June 2024. Chip breaking geometry can help to avoid long tangled chips. It guides and shapes the chip and causes it to snap off. Previously, specially lasered or ground chip breaker geometries were used for this purpose. However, this was associated with increased cost of the inserts. With the new type 105 Supermini, HORN has succeeded in developing a universal boring tool with sintered chip breaking geometry. The tool offers high process reliability due to good chip control. The cutting geometry extends far into the corner radius of the insert. This ensures chip control even at low infeed settings. The geometry can be used universally for different material groups and is suitable for internal, face, copy and reverse turning.
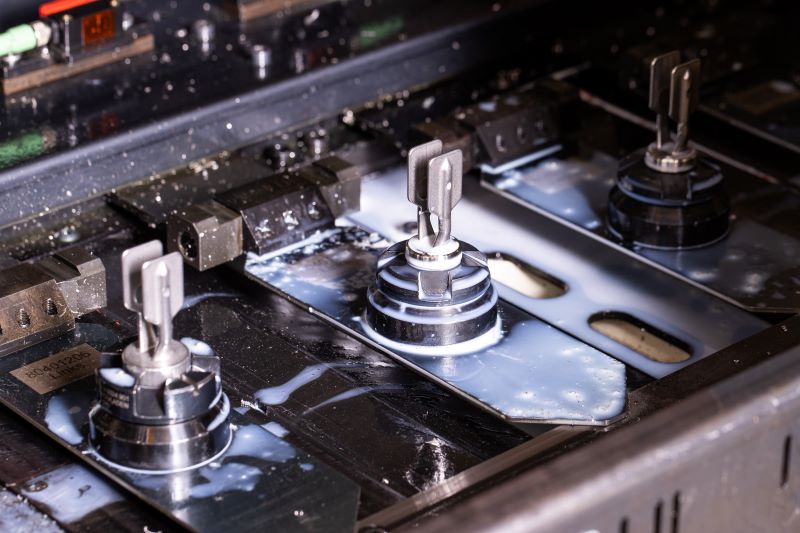
In addition to the geometry, HORN has also optimised the carbide blanks of the inserts to have greater rigidity and an even more stable cutting edge. The coolant supply has also been revised. The new insert is compatible with numerous type 105 clamps. HORN offers the inserts in three lengths (15.0 mm (0.079"), 20.0 mm (0.157") and 25.0 mm (0.394")) and in carbide grade IG35 as standard. The corner radius is 0.2 mm (0.008"). Tool diameter is from 6 mm (0.236"). The wide range of applications of the inserts is also reflected in their cost-effectiveness. The cost of the new Superminis is similar to that of the standard insert without geometry.
Appropriate tool holders
Users can choose the appropriate solution for their machining from a wide range of different types of tool holder. These include round shank holders, square shank holders, interface tool holders and adjustable holders to suit machines from different manufacturers. HORN offers four different solutions for clamping the inserts: Classic screw clamping via a ball pressure screw, clamping via a face clamping element and clamping via a lifting element. For confined spaces, HORN also has in its programme a slim holder system with clamping via a union nut.
Endress+Hauser uses a tool holder with a polygonal shaft and face clamping element for the fully automated production of M forks. These play an important role in measuring equipment. They are used for measuring the level of a liquid. The forks resemble a tuning fork. During operation, they vibrate at a certain frequency. When the fill level in a tank rises and the forks are immersed in the liquid, the frequency of the vibrations changes due to the density of the medium. The sensor thus registers when the fill level has been reached.
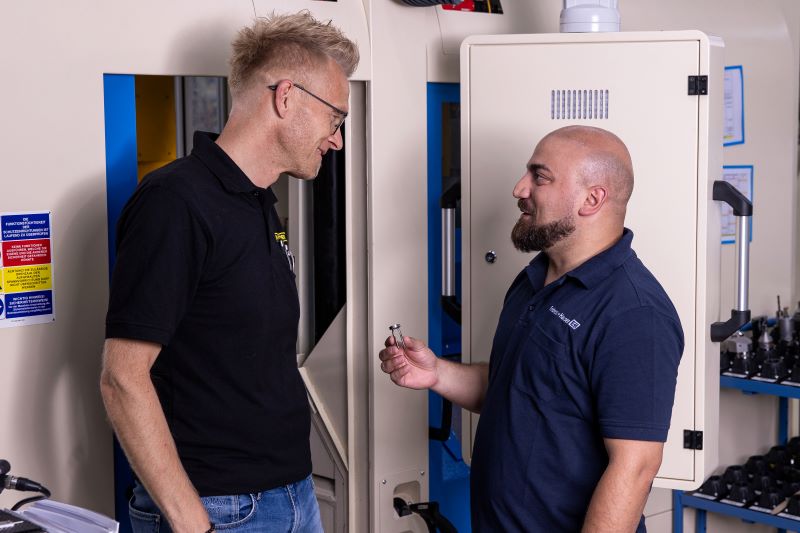
Leading worldwide
Endress+Hauser is a leading worldwide supplier of measuring instruments, services and solutions for industrial process engineering. The company offers process solutions for flow, level, pressure and temperature measurement, for analytical measurements, as well as for data recording and digital communication, thereby optimising processes in terms of economy, safety and environmental impact. Endress+Hauser's customers operate in a wide range of industries such as chemicals, energy and power plants, raw materials, metals and mining, food, life sciences, oil and gas, and water/wastewater.
Endress+Hauser and HORN have been working together for decades. "The new tool has shown us once again why we rely on tools from HORN in our production. In addition to the high level of process reliability, we were able to reduce non-productive times and also increase the service life of the tools," says Oda.