High speed production of a precise bone screw
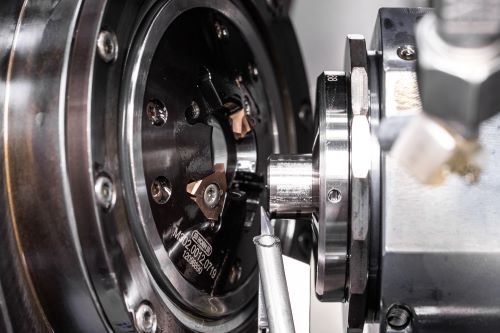
Sports injuries, car accidents or mishaps at home – bone fractures can occur suddenly and unexpectedly. Not infrequently, they are so severe that surgery on the fracture is unavoidable. Depending on the injury, the treating surgeon decides between wires, screwed plates or long bone screws to fix the fracture. Few patients know that bone screws in particular are high-tech medical products. The company hg medical from Raisting in Upper Bavaria is considered one of the leading subcontract manufacturers of these special screws. To produce them, hg medical relies on Swiss-type lathes from Traub and whirling tools from Paul Horn GmbH. In addition to conventional whirling, hg medical uses the high-speed whirling process.
Skull, spine or femur. There is an enormous variety of different screw types for fixing bone fragments. Not all bones are the same. The surgeon selects the appropriate screw depending on the nature of the bone, such as hardness, porosity or bone marrow. In addition to self-locking screws with tapered threads or variable pitches, screws with a through hole are also used, through which bone cement can be injected for stabilisation.
Conventional whirling
"The problem with the conventional whirling process is that the whirling and pre-turning of the diameter must always be done in individual steps. The inserts in the whirling head are not designed to cut the sometimes larger outer diameters of the raw material," says Sebastian Schmid, process developer at hg medical. As a result, the whirling attachment has to be repositioned several times in the threads, depending on the length of the bone screw. This results in so-called entry marks on the surface. Although these are biologically harmless, they could result in a weakness, leading to breakage at that point of the screw if too much stress is placed on it. Furthermore, a flawless surface is desirable as a quality feature of every implant.
Continuous cut
A significant step in the further development of the whirling process is high-speed whirling. The advance was developed through a cooperation between the machine manufacturer INDEX/Traub, hg medical, HORN and a university. In this process, the speed is so high that turning can take place at the same time as whirling. The turning tool positioned in front of the whirling tool reduces the volume of material that would otherwise have to be removed by the whirling tool. The whirling heads used are similar to conventional types: Only the inserts differ in their geometry. The production of single- and multi-start threads is possible with only one set of inserts. The advantage over conventional whirling is, on one hand, a cycle time reduction of up to 30 per cent and, on the other, higher quality of the workpiece. "The time advantage always depends on the application and geometry of the screw. We see a great benefit in the elimination of entry marks, since with high-speed whirling the inserts are in a continuous cut," explains Schmid.
Theoretically, high-speed whirling also has the advantage of increasing the service life of the inserts. This is due to the lower volume of material to be removed by whirling, due to the previous turning operation. "This would be an advantage, for example, when whirling short-chipping materials. However, we process almost 100 per cent long-chipping titanium alloys. When whirling titanium at high speed, the whirling head serves as a chip breaker for the long swarf generated by the simultaneous turning operation," explains Schmid. It diminishes the advantage of the longer tool life in this case. On average, tool life is similar to that achieved with conventional whirling. "We turn or change the inserts in the whirling head in a specific order. The quality of the bone screws is always higher than the maximum service life that has been specified," says Schmid.
High manufacturing precision
Bone screws are subject to strict criteria for manufacturing quality. "The production tolerances, especially for the diameter of the thread, are very tight depending on the screw," says Schmid. Furthermore, a complete absence of burrs must be guaranteed during production. Any burr, no matter how small, poses a potential danger for causing a failure in service. "To achieve the required high quality and specification, the whirling tools and inserts must be manufactured very precisely. A major focus is on axial and radial run-out. The level of accuracy is crucial, especially in the transition between two different threads, or when restarting", explains HORN field service representative, Stefan Benz. HORN grinds the inserts to length tolerances of less than 0.002 mm (0.079 mil). In addition, the insert seats in the whirling head are manufactured with high precision. Another quality feature is the profile of the ground inserts. Defined inner radii of r = 0.025 mm (0.984 mil) with tolerances of +/- 0.005 mm (0.197 mil) are not uncommon in precision grinding of the indexable inserts. For the inserts, HORN whirling tools mainly use the three-edged indexable type S302 variety or the two-edged type S274 insert. All whirling tools are special designs to suit customer requirements.
HORN tool systems have been performing reliably in hg medical's factory for around ten years. In addition to thread whirling tools, the company also relies on grooving and boring systems from HORN: "We sometimes have very difficult tasks during new whirling projects. Luckily, we have a hotline to HORN's design department to discuss each application and develop a tooling solution," Schmid explains and continues: "As a supplier, we offer our customers the highest flexibility and speed and we expect the same from our suppliers and partners. With HORN, we have a tool partner at our side which offers this service and is always available for us."
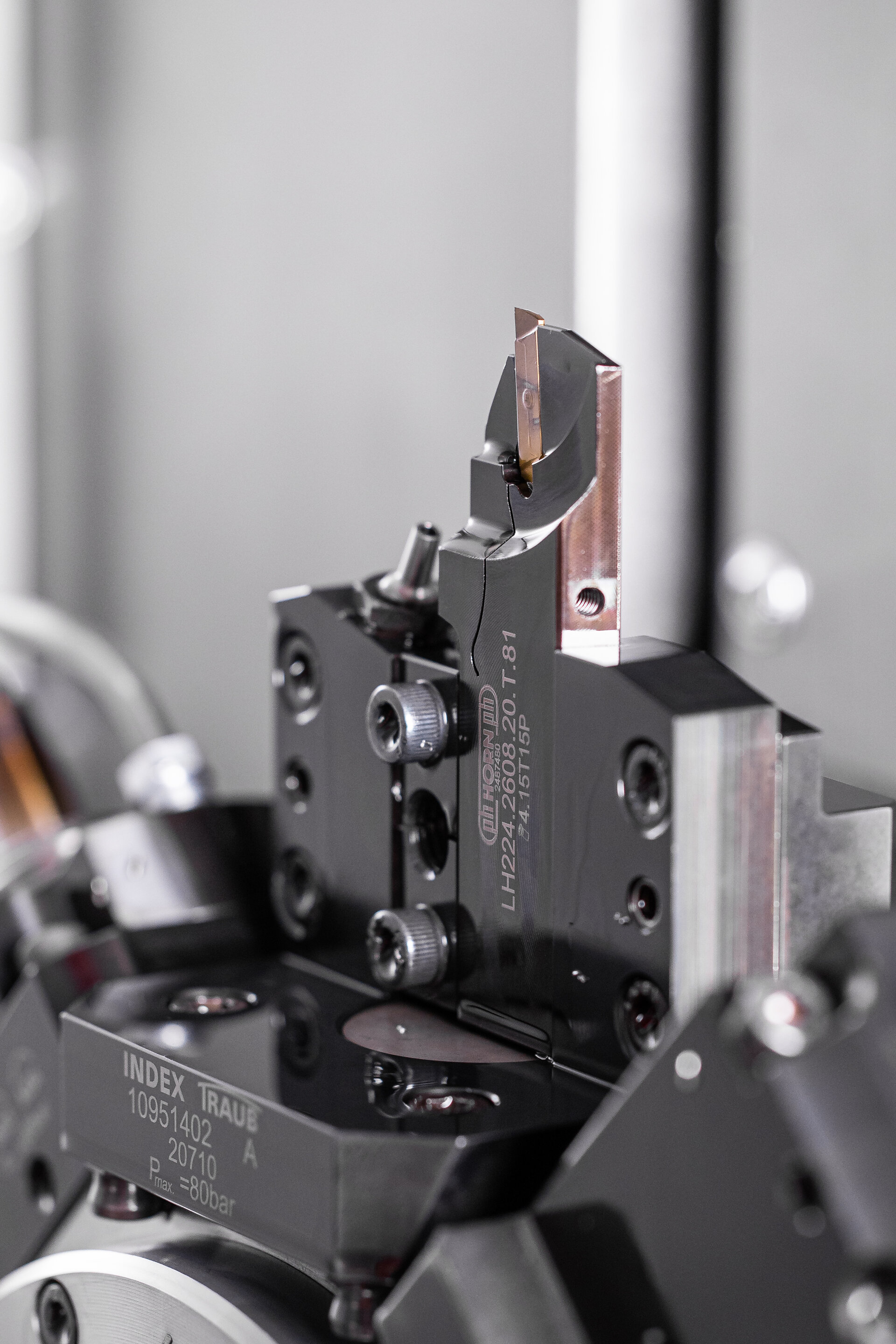