Präzision aus dem Allgäu
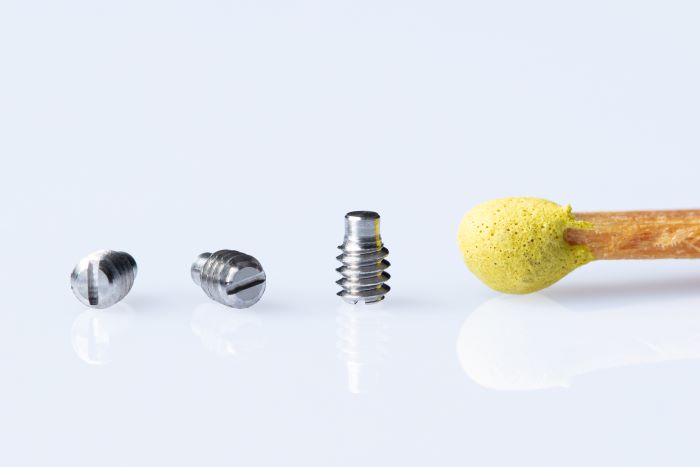
Das Firmenmotto „gscheid gmacht“ steht bei Reinhard Buck nicht nur auf seinem Firmenlogo. Dieses Motto lebt der Unternehmer mit seinen Mitarbeitern in seiner Firma zmtec. In Leutkirch im Allgäu produziert das Unternehmen vom Mikrobauteil bis zu komplexen Baugruppen. Zu den Spezialitäten von Reinhard Buck gehören Kleinstdrehteile ab einem Durchmesser von 0,5 mm. Für die produktive Zerspanung setzt er auf die Werkzeugsysteme der Paul Horn GmbH. „Die große Werkzeugvielfalt und den guten Preis im Verhältnis zur Standzeit sehen wir als großen Vorteil von Horn“, so der Geschäftsführer. Für die Bearbeitung eines Drehschiebers mit einem Durchmesser von 1,6 mm, setzt Buck unter anderen auf das Werkzeugsystem S274 und das Zirkularfräswerkzeug des Typs 606 mit einer Schneidbreite von 0,3 mm.
Absolute Gratfreiheit gefordert
Für den Drehschieber, welcher in einem hydropneumatischen Ventil zum Einsatz kommt, sah Buck das Potential den Bearbeitungsprozess zu optimieren. Von dem Bauteil aus X8CrNiS18-9 (1.4305) fertigt das Unternehmen rund 20.000 Stück pro Jahr. Das Bauteil hat eine Länge von 2,6 mm, eine Gewindegröße von M 1,6 und eine Passung mit dem Durchmesser 1 h8. Zum Einstellen des Drehschiebers im späteren Einsatz muss an der Gewindeseite des Drehteils noch ein Schlitz mit einer Breite von 0,3 mm und einer Tiefe von 0,5 mm gefräst werden. „Die Schwierigkeit bei der Bearbeitung ist unter anderem die geforderte Gratfreiheit des Bauteils. Wenn man einen Schlitz in ein Gewinde fräst, kann man sich schnell vorstellen, dass die Gratfreiheit nicht leicht zu erreichen ist. Man kann so ein kleines Bauteil nicht einfach mit einer Feile entgraten. Das Gewinde wäre sofort unbrauchbar“, erzählt Buck.
Für das Langdrehen der Außenkontur setzt Buck auf das Horn-Werkzeugsystem 274. „Für den Einsatz in dem nichtrostenden Stahl haben wir die Werkzeugbeschichtung IG35 gewählt. Diese Schicht bietet hohe Leistungen bei der Bearbeitung von rostfreien Stählen, Titan- und anderen Superlegierungen“, erzählt der Horn-Außendienstmitarbeiter Gisbert Voß. In der Verbindung mit den Horn-Spanformgeometrien hemmt die Aluminium-Titansiliziumnitrid Schicht die Bildung von Aufbauschneiden durch die geringen Reibwerte. Durch die HiPIMS-Beschichtungstechnologie weist die Schicht sehr glatte Eigenschaften und eine hohe Warmfestigkeit auf. Des Weiteren ist die Werkzeugschicht frei von Schichtdefekten wie beispielsweise Droplets oder anderen Schichtfehlern an der Schneidkante. Der Anwender kann höhere Schnittwerte fahren, die eine kürzere Zykluszeit ermöglichen, was sich positiv auf die Stückkosten auswirkt. Darüber hinaus zeigen sich durch den Einsatz der Schicht höhere Qualitäten der zu erreichenden Oberflächen.
Schlitzfräsen mit dem System 606
Nach dem Drehen der Außenkontur übernimmt ebenfalls eine Schneidplatte des Systems S274 die Fertigung des Gewindes. Das Gewinde M 1,6 hat eine Länge von 2,2 mm und eine Steigung von P = 0,35 mm. Nach dem Gewindedrehen ist der nächste Bearbeitungsschritt das Fräsen des Schlitzes. „Wir haben den Schlitz früher mit einem feinen HSS-Sägeblatt geschnitten. Hier gab es Potential zur Verbesserung“, so Buck. Voß schlug vor, den Schlitz mit dem sechsschneidigen Zirkularfrässystem des Typs 606 zu fräsen. Die ersten Versuche verliefen gleich erfolgreich und Buck ersetzte das HSS Werkzeug durch das Horn-Frässystem. Um die Gratfreiheit nach dem Schlitzfräsen sicherzustellen, wird die Bearbeitung des Gewindedrehens und Schlitzfräsens dreimal wiederholt. „Danach ist das Bauteil gratfrei“, so Buck.