Prozesse beherrschen: Wälzschälen
Vor über einem Jahrhundert reichte Wilhelm von Pittler das Patent zum Wälzschälen von Verzahnungen ein. Im Jahre 1910 war dies eine revolutionäre Idee. Eine breitere Anwendung in der modernen Fertigung findet der Prozess aber erst seit Bearbeitungszentren und Universalmaschinen mit gekoppelten und synchronisierten Spindeln und verfahrensoptimierter Software die Anwendung dieser hochkomplexen Technologie ermöglichen. Das Produktportfolio von Horn umfasst ein breites Werkzeugprogramm zum Wälzschälen unterschiedlicher Verzahnungsgeometrien. Ob Außenverzahnungen, Innenverzahnungen, als Laufverzahnung oder Passverzahnung oder auch regelmäßige Sonderformen, all diese Zahnprofile lassen sich mit den Werkzeugen äußerst wirtschaftlich herstellen.
Das Werkzeugsystem umfasst Werkzeuge zum hochproduktiven Herstellen von Innenverzahnungen, Passverzahnungen und anderen Innenprofilen sowie von Außenverzahnungen mit Störkanten. Die wichtigsten Vorteile des Wälzschälens bei diesen Anwendungen sind die deutlich kürzeren Prozesszeiten im Vergleich zum Verzahnungsstoßen, der Einsatz auf optimierten Dreh-Fräs-Zentren, das Drehen und Verzahnen in einer Aufspannung und der Verzicht auf Freistiche am Verzahnungsende. Darüber hinaus überzeugt die meist produktivere und kostengünstigere Herstellung gegenüber dem Wälzstoßen und Räumen und die im Vergleich zum Nutstoßen vier- bis fünffach kürzere Zykluszeit. Dies zeigt sich auch in der Möglichkeit zur Hartbearbeitung von Verzahnungen ins Volle. Die Wälzschälwerkzeuge sind zum Verzahnen mittlerer bis großer Lose konzipiert. Dabei wird jedes Werkzeug individuell dem Einsatz und dem zu bearbeitenden Werkstoff angepasst, wobei sich die unterschiedlichen Werkzeugschnittstellen an der Zähnezahl und Modulgröße orientieren.
Speziell bei Innenverzahnungen zeigt Horn mit dem Prozess bei größeren Modulen den Vorteil einer kurzen Prozesszeit. Für das Wälzschälen größerer Module sind große und steife Fräs-/Drehzentren erforderlich, welche die entsprechende Synchronisation zwischen Werkstück- und Werkzeugspindel ermöglichen. Je größer das Modul, umso kritischer ist das Thema Maschine in Bezug auf die Steifigkeit. Mit einer Schnittaufteilung auf die linken und rechten Flanken lässt sich dieses Thema werkzeugseitig entkräften. Nach den Erfahrungen mit kleinen Vollhartmetall-Wälzschälwerkzeugen nutzte Horn das gewonnene Knowhow, um auch größere Module abzudecken. Jede Anwendung wird von den Technikern vor der Umsetzung auf die Machbarkeit geprüft und die Werkzeugauslegung sowie die Empfehlungen für den Prozess mit dem Anwender besprochen.
Ein Beispiel hierfür ist ein Unternehmen aus der Aerospace-Branche. Für die Fertigung einer Außenverzahnung benötigte der Anwender rund 20 Minuten. Aufgrund knapper Kapazitäten beim Kunden entwickelte Horn im eigenen Versuchszentrum in mehreren Testreihen die für diesen Wälzschälprozess optimalen Zerspanungsparameter. Die Ergebnisse waren über alle Testreihen reproduzierbar, bei gleichbleibender hoher Qualität. Die Implementierung des Wälzschälprozesses in der Serienfertigung gestaltete sich problemlos. Die ersten Versuche waren sofort erfolgreich. Die in Tübingen ermittelten Schnittdaten für diesen Prozess konnten fast eins zu eins übertragen werden. Die Bearbeitungszeit einer Verzahnung, ohne Entgraten, konnte von über 20 Minuten auf jetzt 7 Minuten reduziert werden. Darüber hinaus entfallen die Umspannzeiten und Transportwege bei gleichzeitiger Erhöhung der Präzision des Bauteils.
Werkzeuge aus Vollhartmetall oder mit Wechselkopf
Das System umfasst Werkzeuge in zylindrischer oder konischer Form für Module von 0,5 bis 2. Die Vollhartmetall-Monoblock-Variante ist mit einem Durchmesser von bis zu 20 mm und in schlanker Bauform lieferbar. Sie kommen bei kleinen Modulen und kleinen Bauteilen zum Einsatz vorzugsweise dann, wenn wegen der Kollisionsgefahr ein schlanker Schaft benötigt wird. Die auf den Anwendungsfall abgestimmten Schneidstoffe und Beschichtungen erzeugen hohe Oberflächenqualitäten am Werkstück. Bei Werkzeugdurchmessern über 20 mm werden Wälzschälwerkzeuge mit Wechselkopfsystem eingesetzt. Die präzise Schnittstelle erlaubt das einfache Wechseln des Schneidkopfes in der Maschine, ohne Ausbau des Halters. Der Halter aus Hartmetall sichert eine hohe Steifigkeit, Verschleißfestigkeit und Präzision. Bei größeren Modulen setzt Horn auf den Einsatz eines Werkzeugträgers bestückt mit Wendeschneidplatten. Speziell beim Werkzeugtyp WSR bietet Horn die Möglichkeit, die innere Kühlmittelzufuhr vor oder hinter die Schneide zu legen. Damit können je nach Anwendungsfall Sackloch-, Durchgangs- oder Stufenbohrungen mit der passenden Kühlung bearbeitet werden.
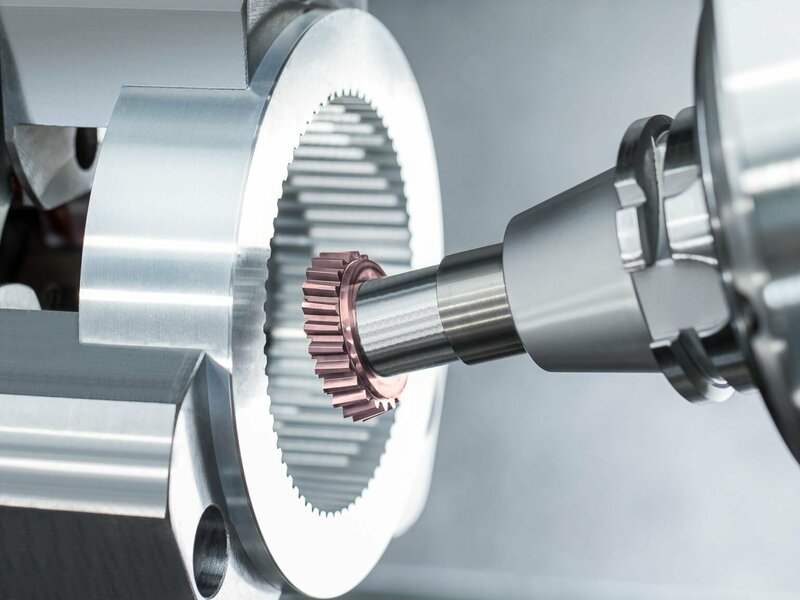