Maîtrise des processus : Skiving d'engrenage
Il y a plus d'un siècle, Wilhelm von Pittler a déposé un brevet pour le skiving des engrenages, une idée révolutionnaire en 1910. Toutefois, ce procédé n'a trouvé une application plus large dans la fabrication moderne que depuis que les centres d'usinage et les centres de tournage universels équipés de broches synchronisées et de logiciels optimisés pour les processus ont rendu possible l'utilisation de cette technologie hautement complexe. La gamme de produits Horn comprend un large éventail d'outils skiving de différentes géométries d'engrenages. Qu'il s'agisse d'engrenages extérieurs, d'engrenages intérieurs, d'engrenages droits, de cannelures ou même de formes de dents spéciales, tous ces profils de dents peuvent être produits de manière extrêmement économique à l'aide d'outils skiving.
Le système comprend des outils pour la production hautement productive d'engrenages intérieurs, de cannelures et d'autres profils intérieurs, ainsi que d'engrenages extérieurs proches des contours d'interférence. Les avantages les plus importants du skiving dans ces applications sont les temps de traitement nettement plus courts que pour le façonnage d'engrenages, son utilisation sur des centres de tournage/fraisage optimisés, le tournage et le taillage d'engrenages en un seul serrage et l'élimination des contre-dépouilles à l'extrémité de la dent. En outre, le processus de fabrication généralement plus productif et plus rentable que le façonnage d'engrenages et le brochage, ainsi que le temps de cycle quatre à cinq fois plus court que l'usinage des rainures de clavette, sont avantageux. Cela se traduit également par la possibilité d'un usinage dur des dents de l'engrenage dans le solide. Les outils skiving sont conçus pour la production de moyennes et grandes séries. Chaque outil est adapté individuellement à l'application et au matériau à usiner, les différentes interfaces d'outils étant basées sur le nombre de dents et la taille du module.
En particulier pour les engrenages intérieurs, Horn offre l'avantage de réduire les temps de traitement lors su skiving de modules plus importants. Les centres de fraisage et de tournage doivent être grands et rigides et la synchronisation entre la pièce à usiner et la broche de l'outil doit être assurée. Plus le module est grand, plus la rigidité de la machine est importante. Avec une répartition de la coupe entre les flancs gauche et droit, ce problème peut être atténué par l'outil. Après avoir acquis de l'expérience avec les petits outils de débitage en carbure monobloc, Horn a utilisé son savoir-faire pour traiter également des modules plus grands. Les ingénieurs de la société évaluent la faisabilité de chaque application avant de discuter avec l'utilisateur de la conception de l'outil et des recommandations relatives aux paramètres du processus, puis de mettre en œuvre le projet.
Une entreprise de l'industrie aérospatiale en est un exemple. L'utilisateur avait besoin d'environ 20 minutes pour produire un engrenage extérieur. En raison de la capacité d'usinage limitée du client, Horn a développé les paramètres de coupe optimaux pour un processus de skiving au cours de plusieurs essais dans son propre centre de test. Les résultats ont été reproductibles dans toutes les séries d'essais, avec une qualité élevée constante. La mise en œuvre du processus de skiving dans la production en série s'est déroulée sans problème. Les premiers essais ont été immédiatement couronnés de succès. Les données de coupe déterminées à Tübingen pour le processus ont pu être transférées presque intégralement. Le temps d'usinage d'un engrenage, sans ébavurage, a été réduit de plus de 20 minutes à 7 minutes. En outre, le temps nécessaire au refixage et à la manipulation a été éliminé, tandis que la précision du composant a été augmentée.
Outils en carbure monobloc ou à tête remplaçable
Le système comprend des outils cylindriques ou coniques pour des modules de 0,5 à 2. La version monobloc en carbure monobloc est disponible dans des diamètres allant jusqu'à 20 mm et dans un design mince. Ils sont utilisés pour la production de petits modules et de petits composants, de préférence lorsqu'un arbre compact est nécessaire en raison du risque de collision. Les matériaux de coupe et les revêtements adaptés à l'application permettent d'obtenir une qualité de surface élevée sur la pièce à usiner. Pour les diamètres d'outils supérieurs à 20 mm, on utilise des outils skiving dotés d'un système de tête interchangeable. L'interface précise permet de changer facilement la tête de coupe à l'intérieur de la machine sans retirer le support. Le support en carbure garantit une rigidité, une résistance à l'usure et une précision élevées. Pour les modules plus importants, Horn mise sur l'utilisation d'un porte-outil avec des plaquettes indexables. En particulier avec le type d'outil WSR, Horn offre la possibilité de placer l'alimentation interne en liquide de refroidissement devant ou derrière l'arête de coupe. Cela signifie que, selon l'application, les trous borgnes, les trous débouchants ou les alésages étagés peuvent être usinés avec le refroidissement le plus approprié.
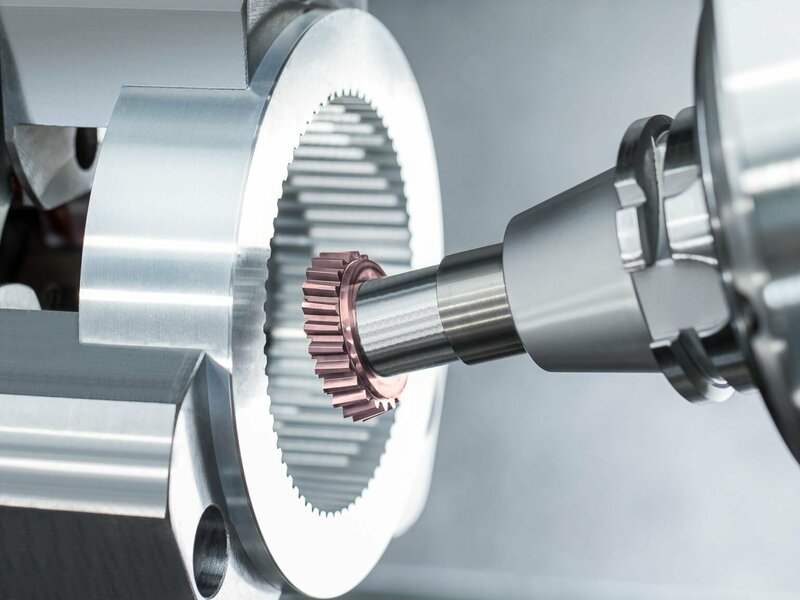