Highend-Verbindungen für extreme Anforderungen
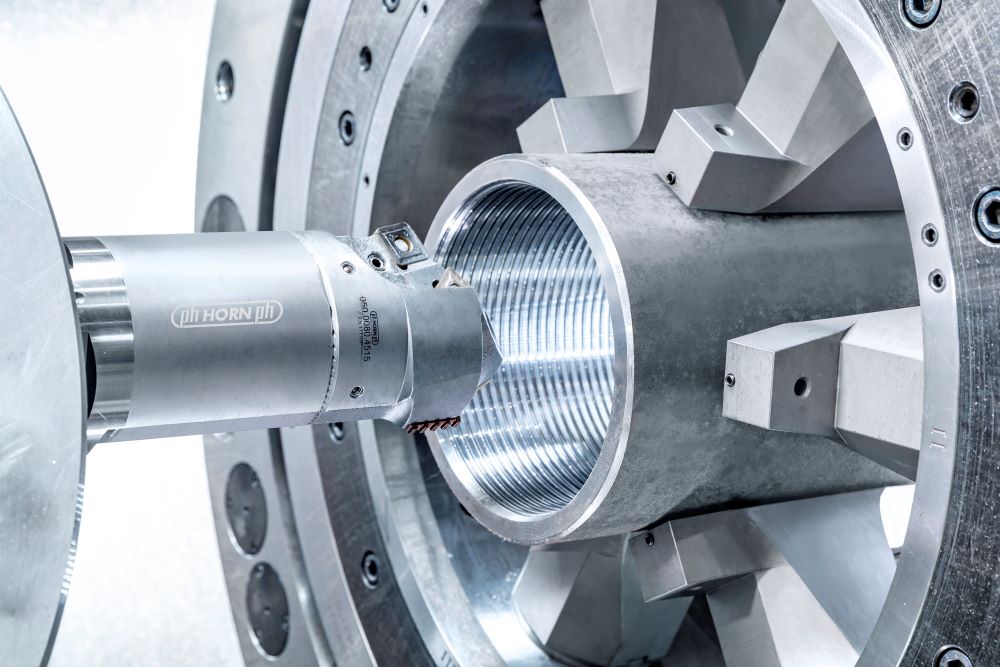
Schweiß, Stahl und harte Kerle: Der Job in der Ölbohrindustrie ist nichts für zartbesaitete Hände. Das Hantieren am Bohrkopf mit peitschenden Zurrketten, tonnenschweren Bohrrohren sowie der ohrenbetäubende Lärm verlangen den Arbeitern viel ab. Bei der groben Arbeit kann sich der Außenstehende jedoch kaum vorstellen, dass für Bohrgestänge und Muffen µ-genaue Präzisionstechnik zum Einsatz kommt. Die wirtschaftliche Fertigung der gasdichten Gewinde verlangt einiges an Knowhow und ein gutes Zusammenspiel zwischen Maschine und Werkzeug. Diese Kombination bietet die SMS group mit den stabilen Muffengewindeschneidemaschinen RMG und die Paul Horn GmbH mit den eingesetzten Werkzeugsystemen.
Im harten Einsatz tragen die „Oil Rigger“ beim Verschrauben des Bohrgestänges keine Samthandschuhe. Dementsprechend haben die Gewinde eine Lebensdauer im Mittel von fünf Schraubzyklen. Während dieser Zyklen muss die gasdichte Verbindung zwischen den Rohren und Muffen sichergestellt sein. Nur mit Premium-Gewinden der höchsten ISO-13679 Norm, lassen sich die unterschiedlichsten und komplexen Anforderungen erfüllen und damit die Erdölvorkommen sicher erschließen. Neben den Premium-Gewinden kommen auch API-und GOST-Gewinde zum Einsatz. „Die Gewindetypen API und GOST finden bei weniger anspruchsvollen Aufgaben ihre Anwendung. Jedoch auch die Herstellung dieser Gewinde unterliegen strengen Qualitätsanforderungen“, erzählt der Horn-Produktverantwortliche Matthias Götze.
Extreme Bedingungen
Sogenannte Sour-Service-Rohre mit Premium-Gewinden halten aggressiven und korrosiven Bedingungen wie Schwefelwasserstoff oder -säure stand. Die großen Vorkommen nahe dem Polarkreis lassen sich nur mit den für die erhöhten Anforderungen entwickelten Premium-Gewinden und den entsprechenden Speziallegierungen des Rohrwerkstoffes erschließen, da die hochfesten und hochlegierten Rohre inklusive ihrer Gewinde für die großen Temperaturschwankungen entwickelt wurden. Im Offshore-Bereich bei den Förderplattformen tragen die Premium-Gewinde dazu bei, dass die Förderstränge der großen Bewegungsintensität dauerhaft standhalten. Nicht immer erfolgen Bohrungen vertikal, sondern müssen geologisch bedingt die Richtung ändern. Auch diese enormen Herausforderungen meistern die OCTG-Bohrgestänge mit Premium-Gewinden.
Die produktive und wirtschaftliche Fertigung der Gewinde verlangt eine stabile Maschine und ein solides Werkzeugsystem, da es sich bei den zu bearbeitenden Werkstoffen um hochfeste und schwerzerspanbare Stähle handelt. „Die zu bearbeitenden Werkstoffe richten sich immer nach der erforderlichen Rohrgüte. Es gibt Stähle, welche sich leichter zerspanen lassen, aber grundsätzlich sprechen wir bei der Gewindeherstellung immer von der Schwerzerspanung“, erklärt Benjamin Henkel, Sales Manager Cold Finishing Long Products der SMS group.
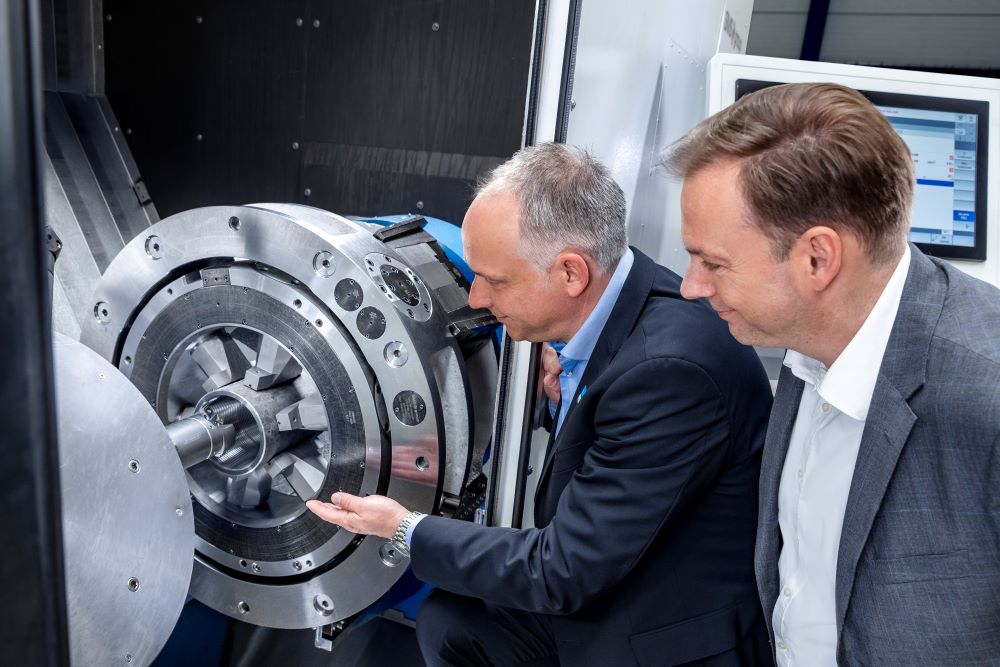
Muffengewindeschneidmaschine
Für die Bearbeitung der Muffen entwickelte die SMS group die RMG Rohrmuffengewindeschneidemaschine. Die Maschine wurde von Anfang an gemeinsam mit internationalen Kunden und Werkzeugherstellern entwickelt. Auf diese Weise ist eine rundum markt- und anforderungsgerechte Lösung entstanden. Dazu brachten die Rohr- und Werkzeughersteller ihre priorisierten Vorstellungen über die Maschine ein. Die Entwicklungsingenieure der SMS group haben auf dieser Basis unterschiedliche Konzepte entwickelt und in einer Nutzwertanalyse ausgewertet. Das Resultat: Eine horizontale Muffengewindeschneidmaschine mit einem Revolverkopf und dem Index-Drehspannfutter für die Premium-Muffenfertigung. Dieses Konzept vereint die wichtigsten Vorteile: Produktivität, Präzision und Flexibilität.
Grundlage der Muffengewindeschneidmaschine RMG ist die felderprobte, erfolgreich etablierte Gewindeschneidmaschine TCG. Von dieser Maschine für Premiumaußengewinde übernimmt die RMG die Kernkomponenten für eine steife Werkzeugmaschine, welche eine hohe Präzision sicherstellt. Beide Maschinen liefern hochwertige Endprodukte nach internationalen Normen wie API oder GOST. So definiert die SMS group neue Standards als ganzheitlicher Anbieter im Bereich der OCTG-Fertigungstechnologie und stärkt die marktführende Position. Die RMG verfügt über sechs Werkzeugaufnahmeplätze, die mit Kombi-Werkzeugen bestückt werden. Dadurch können drei Arbeitsschritte ohne erneutes Werkzeugschwenken ausgeführt werden, was die Prozesszeiten auf ein Minimum reduziert. Hinzu kommt, dass die horizontale Ausführung die Späne-Evakuierung erleichtert und deutliche Vorteile bei der Zuführung von Werkstücken und beim Wechsel der Werkzeuge bietet.
Teure Fehler vermeiden
Ein Highlight der Bedienung ist die integrierte Simulation. Damit kann der Anwender vor dem Beginn des Muffengewindeschneidens den gesamten Prozess simulieren und anhand der Visualisierung prüfen, ob die Programmierung alle Anforderungen und Zielwerte erfüllt. „Die sichtbare Simulation des Werkstücks auf dem HMI schon vor dem ersten Span vermeidet teure Fehler, bevor sie auftreten, und schafft so eine hohe Prozesssicherheit“, so Henkel.
„Die eingesetzten Werkzeuge erfüllen im Drehprozess Höchstleistungen, da die Belastung auf die Werkzeugschneiden sehr hoch sind“, so Götze. Horn setzt bei der Muffenbearbeitung auf Kombiwerkzeuge, um unnötige Werkzeugwechsel einzusparen. Zum Bearbeiten von Innengewinden bei Muffen dient das System 315. Eine dreifach, mit hoher Wechselgenauigkeit, wendbare Schneidplatte mit zwei oder drei Zähnen erzeugt die Gewinde im Vor- und Fertigschnitt. Die Schneidplatten mit einer maximalen Schneidenbreite von 15,5 mm, bearbeiten die Gewinde mit hoher Wirtschaftlichkeit durch lange Standzeiten und in Bezug auf die geringen Kosten pro Schneide. Für eine gute Spankontrolle sorgen integrierte Spanleitstufen. Die Kühlschmierstoffversorgung erfolgt von unterhalb und oberhalb der Schneidplatte. Eine stabile Klemmschraube sorgt beim Schneidenwechsel für hohe Bedienerfreundlichkeit. Um den Maschinenstillstand so kurz wie möglich zu halten, kann das Werkzeug mittels präziser Polygonschaft-Schnittstelle (Größe 80) in wenigen Handgriffen ausgetauscht und durch ein Schwesterwerkzeug ersetzt werden. Die zu wechselnden Schneidplatten können anschließend außerhalb der Maschine ausgetauscht werden.
Das System 315 eignet sich gleichermaßen für API-Buttress-Gewinde, API-Rund-Gewinde, Premium-Gewinde sowie andere Gewindeformen. Durch die reproduzierbaren Standzeiten können Maschinenbediener prozesssicher hochqualitative Gewinde fertigen. Korrekturen sind aufgrund der Präzisionsschnittstelle auf ein Minimum reduziert. Die hohen Standzeiten der Werkzeuge sorgen für wenige Unterbrechungen des Fertigungsprozesses.
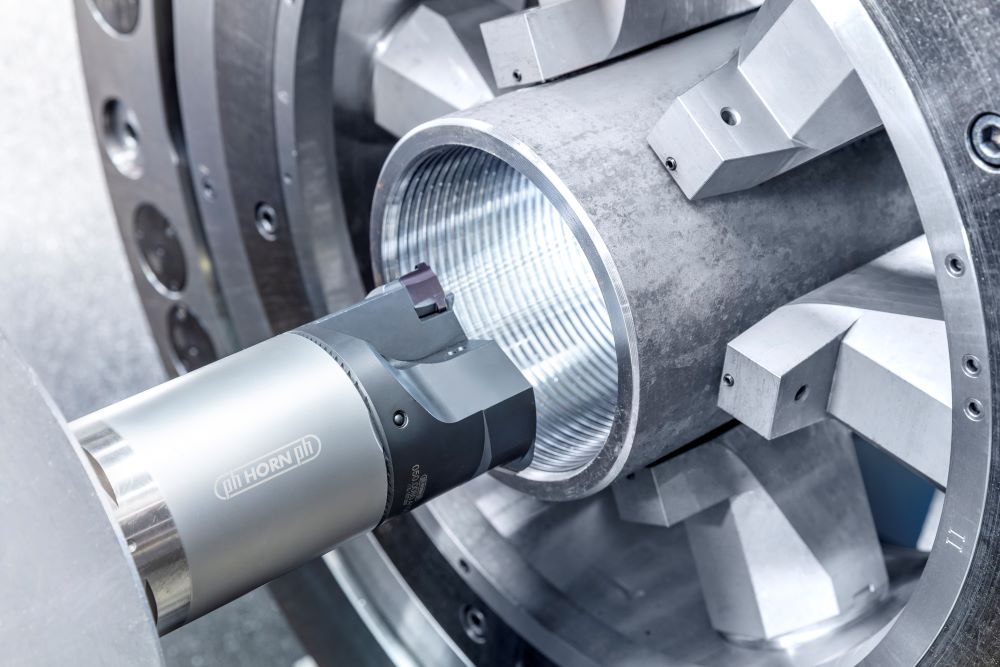
Kombiwerkzeuge im Einsatz
Durch das Kombiwerkzeug lässt sich ein API-Buttress-Gewinde ohne einen Werkzeugwechsel bearbeiten. ISO-Schneidplatten übernehmen im ersten Schritt das Plandrehen und die Fertigung der Außenfase. Danach fertigt eine weitere ISO-Platte den Innenkonus sowie die Innenfase. Anschließend übernimmt die Horn-Wendeschneidplatte das Gewindeschneiden in drei Schnitten. Bei der Fertigung eines Premium-Gewindes kommen zwei Kombiwerkzeuge zum Einsatz. Nach der Außenfase und dem Plandrehen wird der Innenkonus vorgedreht. Anschließend der Konus geschlichtet sowie der Dichtsitz vorgedreht. Alles geschieht mit ISO-Schneidplatten. Nach dem Werkzeugwechsel beziehungsweise der Revolverdrehung übernimmt die Schneidplatte des Typs 315 das Gewindeschneiden in zehn Teilschnitten. Danach übernimmt eine ISO-Schneidplatte das Schlichten der Innenfase und des Dichtsitzes.
„Im Vergleich zu anderen Werkzeugsystemen lassen sich Premium-Gewinde mit nur zwei Horn-Werkzeugen fertigen, wie sonst üblich mit fünf. Durch die Abstimmung des Werkzeughalters und der Schneidplatten des Typs S117 und 315 erzielen wir eine hohe Produktivität und Qualität“, sagt Götze. Durch die hohe Fertigungstiefe, welche über die Rohlingsherstellung in der eigenen Hartmetallfertigung, die Schleiferei und Trägerfertigung bis hin zur Inhouse PVD-Beschichtung geht, ermöglicht Horn kurze Lieferzeiten. Darüber hinaus steht der Werkzeughersteller dem Anwender mit dem eigenen Produktmanagement als Prozessberater und Lösungsanbieter zur Seite. Das Knowhow von Horn bei der Bearbeitung von unterschiedlichen Werkstoffen reicht von leicht zerspanbaren J55-K55, L80 und P110 über Q125 bis hin zu hochlegierten X13Cr und X27Cr.
Die SMS group arbeitet seit mehreren Jahren mit Horn zusammen. Die Zusammenarbeit bewertet Henkel positiv: „Durch das Engagement von Herr Götze sowie der Horn-Konstrukteure sind wir mit den Horn-Werkzeugsystemen deutlich vorangekommen, die vorher so nicht absehbar waren. Ich sehe die Werkzeuge als die optimale Ergänzung für unsere RMG Muffengewindeschneidmaschine.“