Mastering processes: Solutions for micromachining and Swiss-type turning
Outer diameters of 0.1 mm (0.004"), recesses of 0.5 mm (0.020") and feed rates of 5 µm (0.0002") – welcome to the world of micromachining! Screws for hearing aids, balance weights for automatic wristwatches or micro-turned parts for medical assemblies: Manufacturing such parts requires know-how, precise machines and special tools. With cutting depths of down to 0.01 mm (0.0004"), users place very high demands on the tools used. They include shiny surfaces and high dimensional accuracy of the components through the use of low cutting force. HORN has developed suitable solutions with the μ-Finish system for micromachining as well as with other tool systems and manufacturing processes for Swiss-type lathes.
The demands on the tools for micromachining with Swiss-type lathes are high. Due to the sometimes very small cutting depths, the tool edges must be very sharp in order to keep the cutting force as low as possible. However, the ground cutting edges are susceptible to microchipping. Even limited chipping in the range of a few µm at the cutting edge has a negative effect on the surface of the machined workpiece. Furthermore, the surface quality of the rake face plays an important role. To counteract built-up edges, the rake face must have good sliding properties. For this reason, it is finely ground or polished.
Changeover accuracy of 2.5 µm
Clamping of the inserts is another important point in tool design. When machining turned parts of small diameter, the centre height of the tool must be precisely measured. Even slight deviations in centre height have a negative effect on the quality of the workpiece when machining the smallest diameters. In the best case, the machine operator should be able to turn the insert without having to readjust the centre height. With the μ-Finish system, HORN offers a changeover accuracy of +/- 0.0025 mm (0.0001") when indexing a double-edged insert. This is made possible by the precise peripheral grinding of the insert in conjunction with the stable insert seat. In addition, the contact surfaces of the square shank toolholder are also ground, which has an effect on the holistic precision of the HORN system.
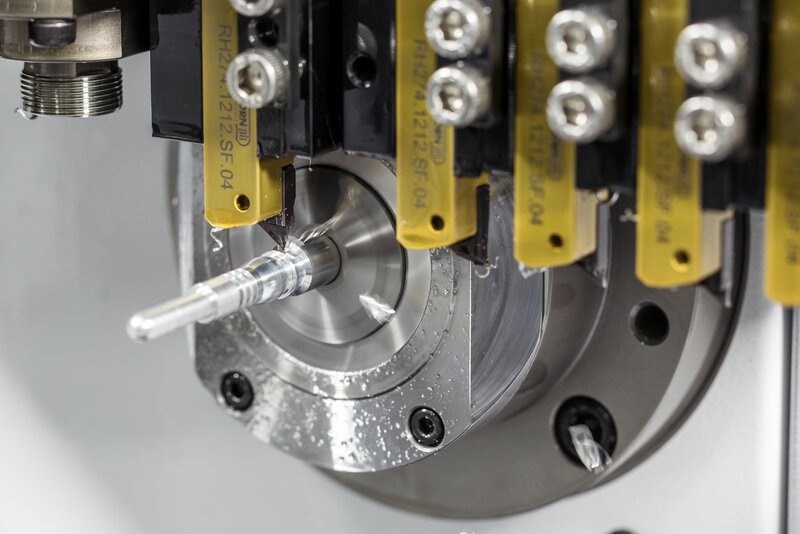
Mastering processes: Solutions for micromachining and Swiss-type turning
Outer diameters of 0.1 mm (0.004"), recesses of 0.5 mm (0.020") and feed rates of 5 µm (0.0002") – welcome to the world of micromachining! Screws for hearing aids, balance weights for automatic wristwatches or micro-turned parts for medical assemblies: Manufacturing such parts requires know-how, precise machines and special tools. With cutting depths of down to 0.01 mm (0.0004"), users place very high demands on the tools used. They include shiny surfaces and high dimensional accuracy of the components through the use of low cutting force. HORN has developed suitable solutions with the μ-Finish system for micromachining as well as with other tool systems and manufacturing processes for Swiss-type lathes.
The demands on the tools for micromachining with Swiss-type lathes are high. Due to the sometimes very small cutting depths, the tool edges must be very sharp in order to keep the cutting force as low as possible. However, the ground cutting edges are susceptible to microchipping. Even limited chipping in the range of a few µm at the cutting edge has a negative effect on the surface of the machined workpiece. Furthermore, the surface quality of the rake face plays an important role. To counteract built-up edges, the rake face must have good sliding properties. For this reason, it is finely ground or polished.
Changeover accuracy of 2.5 µm
Clamping of the inserts is another important point in tool design. When machining turned parts of small diameter, the centre height of the tool must be precisely measured. Even slight deviations in centre height have a negative effect on the quality of the workpiece when machining the smallest diameters. In the best case, the machine operator should be able to turn the insert without having to readjust the centre height. With the μ-Finish system, HORN offers a changeover accuracy of +/- 0.0025 mm (0.0001") when indexing a double-edged insert. This is made possible by the precise peripheral grinding of the insert in conjunction with the stable insert seat. In addition, the contact surfaces of the square shank toolholder are also ground, which has an effect on the holistic precision of the HORN system.
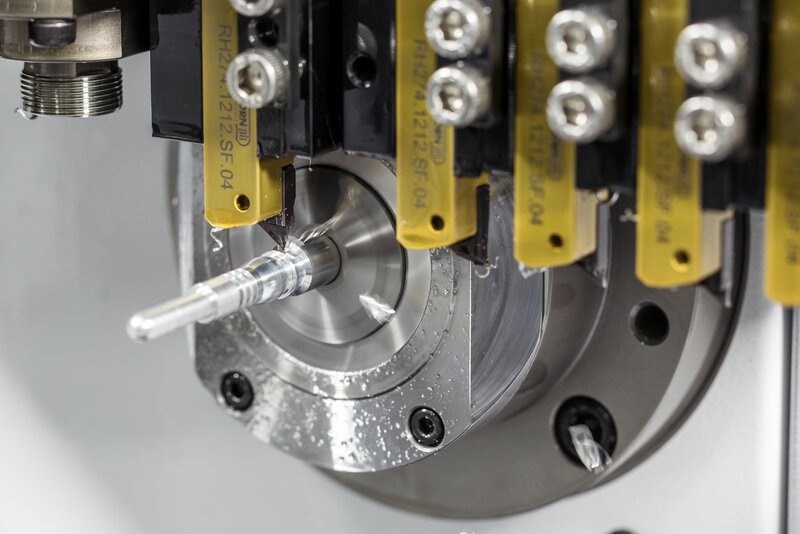