Nine cutting edges for higher metal removal rate
Groove milling, cut-off milling or gear milling: these are just three milling processes that the circular interpolation milling system from Paul Horn GmbH carries out productively. As a true all-rounder, the extensive tool portfolio of this system tackles several other milling processes. It can be used from an inside diameter of 8 mm (0.315") for precise boring, for slot milling of narrow grooves down to a width of 0.25 mm (0.009"), or for milling splines: The system has proven to be a problem solver in numerous standard variants as well as in special designs for individual requirements.
In order to further increase the chip removal volume during milling, Horn is expanding the circular milling system to include inserts with nine cutting edges. The smaller diameters of the system were previously available with a maximum of six cutting edges. Three more teeth offer further advantages. On one hand, the production time is shortened due to the higher cutting feed rates that are possible, while on the other hand, tool life is increased. In addition, the inserts run more quietly and with less vibration than inserts with fewer teeth. These advantages, in addition to the high milling performance of the tool system, contribute to higher overall efficiency and a reduction in tool costs.
The new nine-edged milling systems M911, M913 and M928 are stocked in cutting widths from 1.5 mm (0.059") to 3 mm (0.118") as standard. The maximum milling depth is 3.5 mm (0.138") (M911), 4.5 mm (0.177") (M913) and 6.5 mm (0.256") (M928). The inserts are available with different coatings to suit the material to be machined. Due to its mass, the solid carbide tool shank ensures vibration damping during milling. All variants of the tool shanks are equipped with an internal coolant supply.
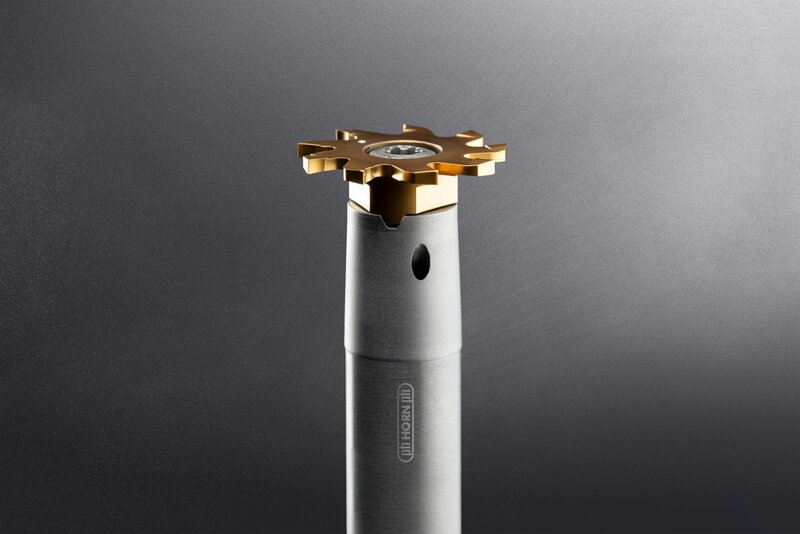