Mastering processes: Ball race milling
High milling performance, long tool life and continuous optimisation of the tool systems used: Paul Horn GmbH demonstrates its know-how in tool technology for ball race milling for constant-velocity joints. Even with high infeed depths and feed rates, manufacturing tolerances are in the micron range. Horn achieves these results with the SX type interchangeable head system, very precise grinding of the cutting edge profile and the passion to always get the most out of the milling process.
Constant-velocity joints, also called homokinetic joints, are used in every automobile. The joint serves to evenly transmit the torque and angular velocity from the drive shaft to a second shaft mounted at an angle to it. Constant velocity joints transmit the rotary motion uniformly to the next shaft. The joints are most widely used in vehicle construction for the transmission of power from the gearbox to the drive wheels. Constant velocity joints can transmit rotary movements up to an angle of 50 degrees. In addition to fixed constant velocity joints, double offset joints are also used. In addition to angular movement, they allow axial movement so that power transmission is not interrupted when the wheels are turned and the suspension moves up and down.
The heart of a homokinetic joint are the ball bearings, which roll in precisely milled ball races. They have a very tight manufacturing tolerance and a high surface finish. The tolerances held and the manufacturing quality achieved determine the service life of the joints. The form tolerances to be achieved in the production of the raceways are also in the micron range. Fixed and double offset joints are used in a drive train. The ball races are milled into the pivot pin, the knuckle joint and the inner race.
The Horn tool system SX is the further development of Horn's 42X family of ball nose milling cutters. The 42X system was limited in its milling depth by the centric clamping screw. Further development resulted in the interchangeable SX head system. The cutter head is connected to the contact surface of the tool body via a stable, robust but nevertheless highly accurate thread. This interface has several advantages: High stability due to the substantial thread, rigid support due to the large contact surface and precise positioning on changeover, which is always in the middle of the tolerance band. In addition, exchanging the cutter head is simple and user-friendly.
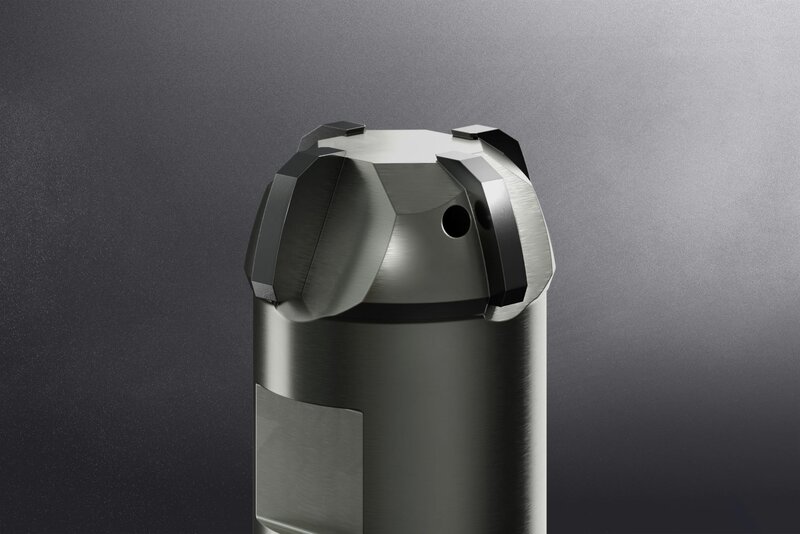