Tourbillonnage pour une excellente qualité sonore
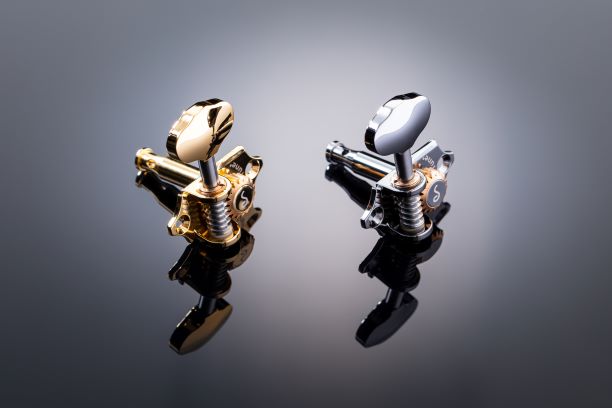
La musique rend les gens heureux un moment et peut les faire pleurer le lendemain. Cela peut aider les gens à atteindre des performances optimales dans le sport ou les rendre anxieux. Mais une chose que la musique ne fait jamais, c'est de vous laisser froid. Et la guitare évoque plus d'émotion que pratiquement n'importe quel autre instrument. Que ce soit autour d'un feu de camp ou lors d'un concert de rock dans un stade, le fonctionnement des guitares est toujours le même. Schaller GmbH, basée près de Nuremberg, s'occupe du fonctionnement de cet instrument à cordes pincées depuis plus de 75 ans. Pendant ce temps, l'entreprise est devenue le leader mondial du marché des pièces de guitare. Avec des machines modernes, l'équipe dirigée par le directeur de l'usine Dominik Weininger tourne et fraise les composants précis nécessaires pour produire une excellente qualité sonore. Il s'appuie également sur le système de tourbillonnage à refroidissement interne de Paul Horn GmbH, basé à Tübingen.
La vis de réglage à filetage hélicoïdal est un élément central de la tête de la machine. Nicole Gawatsch, chef du département de tournage et de fraisage CNC, a vu dans ce filetage un potentiel d'amélioration. "Auparavant, nous fraisions le filet de la vis sans fin à l'aide d'une fraise latérale. Le temps d'usinage nécessaire était trop long pour nous et nous devions souvent reprendre la pièce et la resserrer à la main", explique Mme Gawatsch. " Nous avons pris connaissance du tourbillonnage à jet à refroidissement interne de HORN lors de l'AMB 2018 et avons immédiatement contacté notre représentant commercial HORN ", poursuit le directeur de l'usine Weininger. Les premières discussions avec HORN sur le nouveau système de tourbillonnage et le lancement du projet ont rapidement suivi.
"L'unité de tourbillonnage fonctionne 24 heures sur 24 et 7 jours sur 7 dans la machine depuis plus d'un an. Nous sommes très satisfaits du système d'outils", déclare le directeur de l'usine, M. Weininger. Le changement réussi du processus se reflète également dans le temps de traitement. Auparavant, Gawatsch avait besoin d'environ une minute pour fraiser le fil de la vis sans fin. Le tourbillonnage conventionnel prend 40 secondes. "Avec le tourbillonnage à refroidissement interne, nous avons divisé par deux le temps d'usinage, qui n'est plus que de 20 secondes par pièce. Compte tenu du nombre incroyablement élevé de composants que nous traitons chaque année, il s'agit d'une économie énorme", explique M. Gawatsch. Outre la réduction du temps d'usinage, la qualité de la surface des composants finis est également nettement améliorée. En outre, la durée de vie des plaquettes indexables a été multipliée.