Yeni PCD frezeleme programı
Paul Horn GmbH’nin yeni PCD frezeleme programı, alüminyumun verimli ve güvenilir işlenmesine odaklanarak, frezelerden karmaşık ve modüler kombinasyon takımlara kadar geniş bir standart ve özel takım yelpazesi sunmaktadır. DM20–DM33 serilerindeki PCD frezeler, evrensel çok yönlü takımlar olup, teknik özelliklerine bağlı olarak geniş uygulama alanlarına uygundur.
DM20
DM20 serisindeki PCD frezeler evrensel çok yönlüdür ve geniş uygulama alanlarına uygundur. Merkez kesme özelliğine sahip çift kesitli PCD uçlu freze takımları, işleme uygulamalarının hemen tamamını kapsar ve özellikle hafif metaller ve mühendislik plastikleri gibi metal olmayan malzemeler için evrensel olarak uygundur. Seri, kuru veya ıslak işleme için özel olarak uyarlanmış gövde tasarımıyla tamamlanır. Farklı PCD substratları ve modern, kişiye özel kesme kenarı hazırlama teknolojileri, verimli işleme süreçlerinin yanı sıra güvenilir yüksek performans ve uzun takım ömrü sağlar. HORN, yarı standart bir takımla müşteri taleplerine hızlı ve esnek uyarlama imkanı da sunar.
DM25
8 mm (0.314”) ile 18 mm (0.708”) arasında değişen kesme kenarı uzunluklarına sahip DM25 ürün gamı, yüksek kesme ilerleme hızlarının gerektiği dış ve iç konturlarda kontur ve finisaj frezeleme işlemleri için özellikle uygundur. Çoklu kesitli tasarım, işleme çevrim sürelerini önemli ölçüde azaltır. R serisi, iç soğutmalı olarak hafif metaller için tercih edilirken, pozitif kesme açısına sahip C serisi aşındırıcı malzemelerden grafit ve fiber takviyeli plastiklere kadar işleme için uygundur.
DM27
Modern fiber takviyeli kompozitler daha hafif, daha güçlü ve daha stabil olup, endüstriyel uygulamalarda giderek önem kazanmaktadır. Bu aşındırıcı malzemelerin işlenmesinde bileşen kenarlarının kalitesi ön plandadır. Tüylenme, tabakalanma veya kenar kırılması, bu bileşenlere özgü ve aşınmaya bağlı koşulları kontrol etmek için takım geometrisi ve kalitesi üzerinde sıkı kriterler oluşturur. İnce cidarlı bileşenlerde veya panel trim kesimlerinde titreşim riski, aşağı veya yukarı freze seçenekleri dikkate alınarak, stabil frezeleme için ek bir faktördür. Pozitif-negatif uç düzenlemesi, iç soğutma ve merkez kesme özelliği ile DM27 serisindeki takımlar, evrensel frezeleme uygulamaları için koordineli bir paket sunar.
DM30
DM30 serisindeki freze takımları, uzun bileşenlerin kesilmesi için özel olarak tasarlanmıştır. Spiral tasarımlı PCD uçlu frezeler, düzgün kesme hareketi ile etkileyicidir. Segmentli tasarım, kesme kuvvetlerini ve işleme gürültüsünü azaltır. PCD uçların hassas konumlandırılması ve düzeni, çapaksız yüksek yüzey kalitesi sağlar. Takımlar çevresel frezeleme, temizleme veya dairesel frezeleme işlemleri için uygundur; küçük ve orta talaş derinliklerinde kullanılabilir ve kesme kenarı uzunluğunun maksimum kullanımına yönelik finisaj işlemlerinde etkilidir. Kesme kenarları yüksek kaliteli ve çapaksızdır.
DM33
Yüksek mukavemetli ve dövme alüminyumdan yapılan bileşenler işlenmesi zor malzemelerdir ve takımdan yüksek performans beklerler. Klasik alüminyum dökümün aksine, ekstrüde ve dövme alüminyum, silikon eksikliği ve sıkışmış malzeme yapısı nedeniyle uzun talaş oluşturur. Ayrıca, oluşan talaş kenarları ve takıma uygulanan ortalamanın üzerinde yük vardır. DM33 serisi ile HORN, özel bir frezeleme konsepti sunar. Yüzey frezeleme veya eğik kesim işlemlerinde, takımlar ön işlem yapmadan yüksek giriş değerleri ile katı malzemeye helisel giriş yaparak delikler veya cepler açmak üzere tasarlanmıştır. 12 mm (0.472”), 16 mm (0.630”) ve 20 mm (0.787”) çaplarında takımlarla delikler, oyuklar, cepler veya profiller güvenilir ve ekonomik şekilde üretilebilir. Takımlar merkezi soğutma kanalı ile tasarlanmış olup, derin işleme işlemlerinde bile güvenilir talaş akışı sağlar. Daha büyük delikler için DG-V serisinde farklı uzunluktaki takım tutucularla birlikte daha büyük vidalı çaplar mevcuttur.
Ultra sert kesme malzemeleri alanındaki bu geniş HORN portföyü, kullanıcılara işleme uygulamaları için uygun, güvenilir takım çözümünü sunma imkanı verir. Odak noktası maliyet etkinliği ve üretkenlik olup, HORN teknolojisi, esneklik ve güvenilirlikle birleşmektedir.
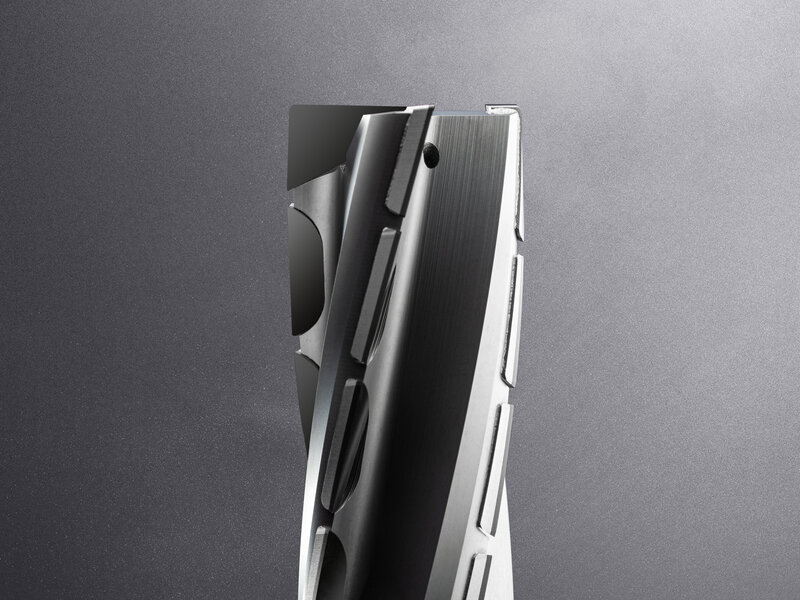