Modern malzemelerin verimli işlenmesi
Kurşunsuz alaşımların işlenmesindeki en büyük sorun, ister pirinç ister kolay işlenen çelik olsun, güvenilir talaş kırmanın olmamasıdır. Peki insan sağlığı için toksik olan alaşım bileşeni kurşunun etkisi tam olarak nedir? İşleme sırasında yumuşak metal, alaşımda önceden belirlenmiş kırılma noktaları oluşturur; çünkü kurşun, alaşım yapısında küçük yuvalar veya dahil olmalar oluşturur. Bu yapılar, işlem sırasında iyi talaş kırma ve düşük kesme kuvvetleri sağlar. Ayrıca, ağır metal bir yağlayıcı film gibi davranarak takım aşınmasını olumlu yönde etkiler.
Geçiş süreci başlangıçta zorluydu. Kurşun alaşımlı malzemelerin iyi kesme özellikleri kayboldu. Buna ek olarak, kesme kenarında aşınma belirgin şekilde arttı. Bu durum, çelik sektöründen alınan talaş kırıcı geometrilerle kanal açma ve boyuna tornalama ile özel lazer kesim geometrileri sayesinde düzeltildi. Yapılan kapsamlı araştırmalar, özellikle orta sertlikteki çelikler için tasarlanmış talaş kırıcı geometrilerin kurşunsuz malzemelerde çok iyi çalıştığını göstermektedir.
İç tornalamada ise uyarlanmış geometriler güvenilir talaş kırmayı sağlar. İç işleme sürecindeki en büyük zorluklardan biri uzun talaşlardır. Bu durum genellikle delik işleme sırasında ortaya çıkar. Uzun talaşlar takım etrafına sarılır, delikleri tıkar veya en kötü durumda takım kırılmasına yol açar. Daha önce bu amaçla özel olarak lazerle işlenmiş veya taşlanmış talaş form geometrileri kullanılmıştır. Ancak bu, kesici uca ek bir maliyet getirmiştir. Horn, yeni Tip 105 Supermini ve I geometrili Tip Mini ile sinterlenmiş talaş form geometrisine sahip evrensel kanal tornalama takımları geliştirmeyi başarmıştır. Bu takımlar, iyi talaş kontrolü sayesinde yüksek işlem güvenilirliği sunar. Kesme kenarı geometrisi, uç köşe yarıçapına kadar uzanır ve küçük talaş derinliklerinde bile talaş kontrolünü garanti eder. Bu geometri, farklı malzeme gruplarında evrensel olarak kullanılabilir ve iç, yüzey, kopya ve ters tornalama için uygundur.
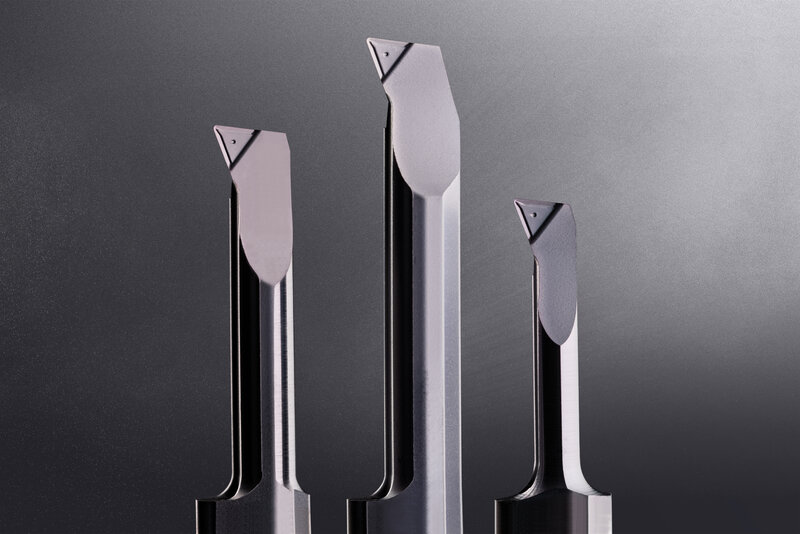