Cubic boron nitride for tough cases
Paul Horn GmbH is expanding its tool portfolio for machining hard materials and other steels.
Tools tipped with cubic boron nitride (CBN) offer optimised machining of nickel-based and other superalloys as well as powder metallurgical and hardened steels. The ultra-hard cutting material CBN demonstrates its strengths in smooth cutting and interrupted cutting when hard turning and grooving. By including extensions in the standard range for the Supermini 105, Mini 11P, 229 and 315 systems, Horn offers the user fast delivery of the desired tool systems from stock.
The Supermini system is available in left and right hand versions with different corner radii. The CBN-tipped variants are suitable for internal machining from a diameter of 2 mm (0.079"). Different projection lengths of the solid carbide bodies are also available. Tools in the Mini family can be used from an internal diameter of 6.8 mm (0.268") and are also available in left and right hand versions. The single-edged tool type 315 is suitable for external grooving operations from a groove width of 0.5 mm (0.012"). In the cutting insert system 229 the previous CBN substrate CB 50 is replaced by the higher-performance substrate CB 35. The cutting inserts are available with two different corner radii and cutting widths from 3 mm (0.118") to 6 mm (0.236").
After diamond, CBN is the second-hardest material known to man. Tools made from CBN wear much more slowly than other cutting materials when used properly. This makes it possible to achieve higher dimensional and shape accuracy and also means that hard materials (steel up to 70 HRC) can be machined reliably. There are no different types of CBN. Differentiation is made by the CBN volume fraction, the fillers, the grain size and the ceramic/metallic binder phase (cobalt/nickel). This results in different CBN substrates. Hard machining with CBN cutting materials is usually done without coolant. This is possible as the cutting material has a high heat resistance and the high temperature within the chip formation zone has a positive effect. An insufficient supply of coolant or interruptions in cutting lead to high, thermally induced stresses in the structure of the indexable insert. This can lead to cracks in the structure and possibly even destroy the indexable insert. During hard machining, most of the heat generated in the shear zone is dissipated via the chip. While carbide suffers a significant loss of hardness at around 800 degrees Celsius (1,472 °F), the hardness of CBN remains almost unchanged, even at temperatures up to 1,200 degrees Celsius (2,192 °F). Another significant advantage is chemical resistance, particularly at the prevailing temperatures.
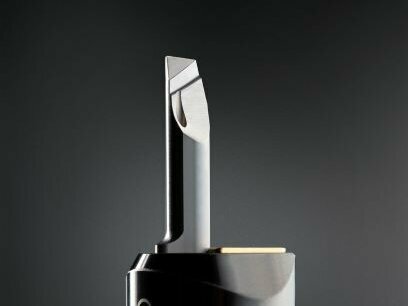
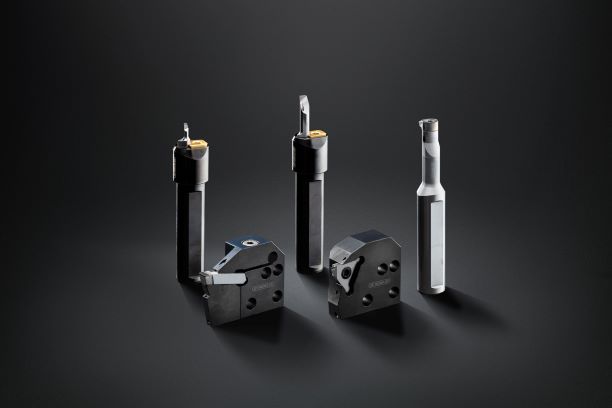