Stratégie vers l'excellence : L'industrie 4.0
Paul Horn GmbH, à Tübingen, poursuit sans relâche le développement et la numérisation de l'ensemble de sa chaîne de valeur. In order to accelerate digitalisation in the production environment, Horn has developed a scalable standard solution for connecting existing and new systems. Thanks to the optimised networking of the systems, Horn customers benefit in many areas including even better delivery performance.
En 2018, Horn a lancé un projet de numérisation et de mise en réseau des systèmes existants (retrofit). Les objectifs comprennent l'introduction d'une architecture orientée services (SOA) dans la production et la standardisation des données des actifs des services d'administration.Le concept développé doit également servir de base à la connexion des systèmes futurs. Lors de l'étude préliminaire du projet, il est rapidement apparu que l'ensemble de l'architecture informatique de la production devait être pris en compte pour une numérisation durable. Le concept de ce que l'on appelle les capsules de production décrit à la fois l'approche méthodique pour remplacer la pyramide d'automatisation et une architecture générique de l'industrie 4.0 composée d'infrastructures (matériel, réseaux, emplacements), d'applications, d'interfaces, de technologies et de processus.
La capsule de production est une unité fonctionnelle composée d'éléments nécessaires à la réalisation d'un objectif spécifique. Par exemple, une capsule de production dans le domaine de la rectification se compose d'au moins une machine CNC et est complétée par l'automatisation, un ordinateur pour l'edge computing ou plus si nécessaire. Le concept ne limite délibérément pas la portée d'une capsule, ce qui signifie qu'il peut être appliqué de manière générique. Cela va de capteurs intelligents individuels à des zones de production entières.
Outre la délimitation logique, le concept Industrie 4.0 aborde également l'encapsulation des données qui en résultent. Il s'agit principalement de la dissimulation ciblée d'informations contre tout accès non autorisé et de la définition d'interfaces standard (modèle de la boîte noire). Les personnes extérieures ne peuvent pas communiquer avec les différents composants d'une capsule. Ils ne voient que les données et les fonctions qu'elle met délibérément à disposition. Avec un modèle de données sémantique, cela crée la base de la standardisation et de l'orientation de la production vers les services. Avec l'utilisation d'OPC UA, une norme appropriée est disponible pour réaliser le concept tout en tenant compte de la sécurité informatique.
Techniquement, l'encapsulation a déjà lieu au niveau du réseau grâce à l'utilisation de routeurs physiques ou virtuels avec des pare-feu locaux. Le partenaire de communication central d'une capsule qui peut être atteint de l'extérieur est appelé un intégrateur. La tâche d'un intégrateur est de soutenir la connexion des composants - par exemple en traduisant les protocoles propriétaires en OPC UA et en harmonisant et agrégeant les données. La communication (M2M) des autres composants au sein d'une capsule n'est pas affectée. L'intégrateur fournit également des services locaux pour le prétraitement des données collectées ou pour la visualisation sur le web.
Horn a déjà équipé la majorité de ses machines de capsules de production. La flexibilité et l'évolutivité du concept permettent de connecter rapidement une grande variété de systèmes. Le fabricant d'outils de précision compte environ 600 machines et systèmes en production dans le monde entier. Il y a également des appareils provenant d'autres domaines, tels que les systèmes de gestion des bâtiments. La valeur ajoutée est évidente dans les divers défis auxquels sont confrontées les différentes unités commerciales. Les coûts d'administration sont réduits pour l'informatique, car la télémaintenance est automatisée et l'opérateur du système peut l'activer à l'aide d'un interrupteur à clé. La sécurité informatique est renforcée par l'isolation des systèmes du côté du réseau - une seule machine défectueuse n'a aucun effet sur le reste de la production. L'ingénierie mécanique et la maintenance internes bénéficient d'un stockage gérable et de la disponibilité à long terme du matériel installé et standardisé. Les données enregistrées peuvent être automatiquement enregistrées et évaluées grâce à la normalisation et à la description sémantique. Les données relatives à la puissance et à la machine, telles que la vitesse de la broche ou les températures, sont enregistrées de manière centralisée par l'intégrateur et mises à disposition de manière standardisée via OPC UA. La solution permet une visualisation basée sur les modèles de données. Cela permet, par exemple, d'avoir une vue d'ensemble de l'état de toutes les machines d'une ligne de production. André Hoettgen, architecte Industrie 4.0 chez HORN : "La mise en réseau des systèmes permet d'optimiser les processus existants et de repenser les futures technologies de production. L'intelligence collective améliore les performances de livraison et ouvre la voie à des outils encore plus polyvalents."
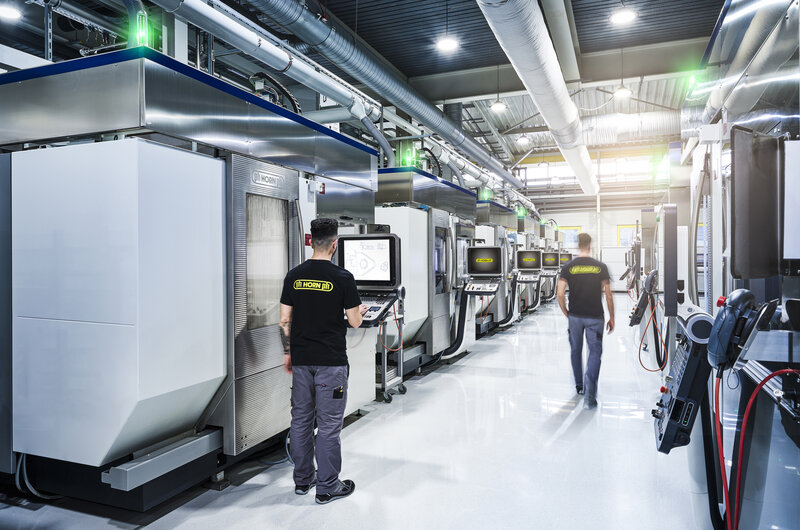