Fraisage à haute degré de brillance à la place du polissage
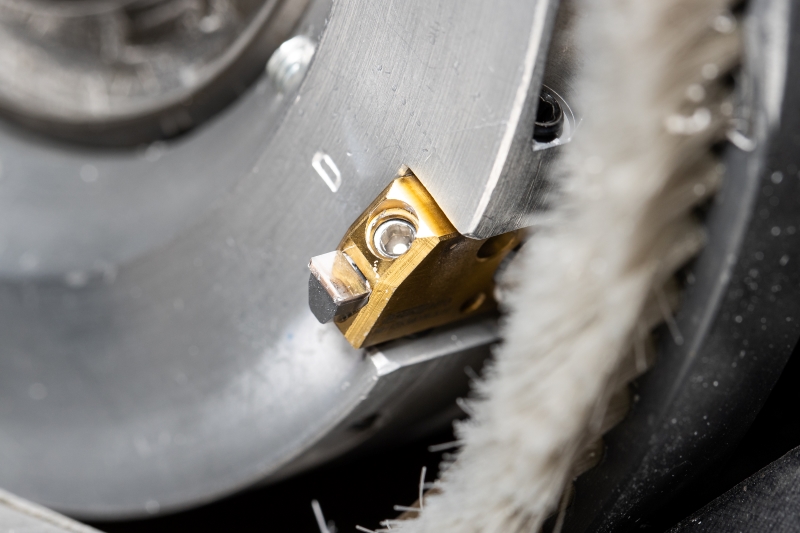
Une application de Germering, en Bavière, montre qu'il n'est pas nécessaire d'utiliser des machines spéciales pour fraiser des surfaces plastiques très polies. L'entreprise Enggruber, en collaboration avec Paul Horn GmbH, a clairement démontré que cela fonctionne également avec des machines conventionnelles. Les outils sont en diamant monocristallin, ce qui garantit une qualité de surface de l'ordre du nanomètre lors de l'usinage de haute précision. « La qualité de l'arête de coupe de l'outil est le facteur décisif pour la finition de la surface qui peut être obtenue », explique Aribert Schroth, spécialiste des outils HORN et chef de produit pour les matériaux de coupe à dureté élevée.
À Germering, à l'ouest de Munich, dans un bâtiment industriel d'apparence discrète, on ne devinerait jamais que des écrans en verre acrylique de haute qualité y sont produits pour l'élite de divers secteurs industriels. Dans le secteur de l'affichage, Thomas Enggruber est connu sous le nom de « Red Adair », le célèbre pompier. Grâce à ses nombreuses années d'expérience, il éteint les incendies et résout les problèmes avant qu'ils ne deviennent sérieux. Le portefeuille d'Enggruber comprend des présentoirs de produits cosmétiques, des prix et des trophées, des meubles et d'autres produits en acrylique et en plexiglas. Il fabrique également ses propres produits dans son atelier. Il produit par exemple des cadres photos avec un effet 3D et d'élégantes planches à découper en plastique cristallin.
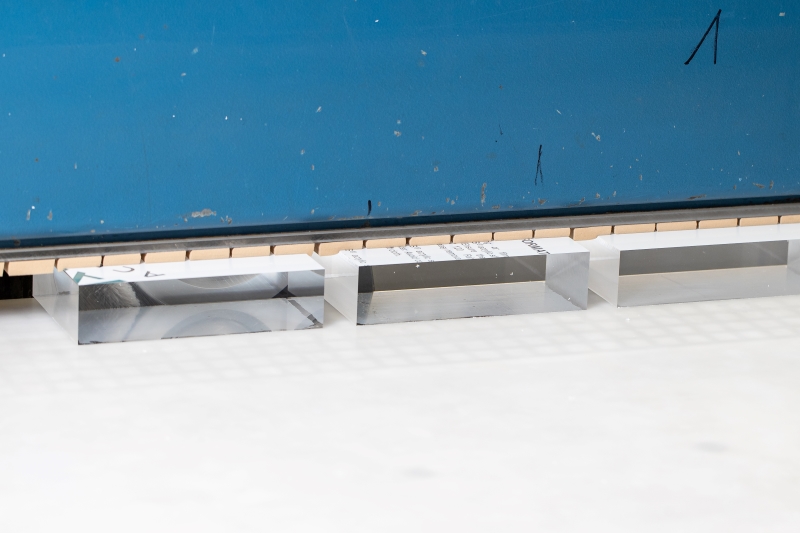
Feu et flamme
« Nous examinons attentivement les processus de notre usine et sommes constamment à la recherche de possibilités d'optimisation », explique M. Enggruber. L'un des principaux objectifs était de traiter les bords des blocs ou des panneaux de verre acrylique. "Nous recevons la matière première sous forme de pièces sciées. Dans le processus de production des grands panneaux, les deux côtés sont déjà transparents et recouverts d'un film protecteur. Cependant, lorsque les panneaux sont coupés sur mesure, les quatre bords sont rugueux à la livraison", explique M. Enggruber. Il existe plusieurs façons de rendre ces bords rugueux clairs comme du cristal. D'une part, le verre acrylique peut être poli à la flamme. Il s'agit de faire passer avec précaution la flamme d'un chalumeau à acétylène sur les bords. On obtient ainsi une surface claire, mais qui n'est pas parfaitement plane. En outre, des fissures capillaires peuvent apparaître sur les bords. D'autre part, les bords peuvent être polis à la main à l'aide d'une machine à polir, également connue sous le nom de lustreuse. Le polissage permet d'obtenir une finition brillante, mais nécessite beaucoup de temps, surtout pour les grandes quantités.
Un autre procédé d'usinage des arêtes est le fraisage avec des outils à pointe en diamant monocristallin (MCD). Enggruber utilisait ce procédé depuis un certain temps, mais les résultats de la surface ne lui donnaient pas entière satisfaction. Il était également gêné par la manipulation et le réglage fastidieux des systèmes d'outils utilisés jusqu'alors. "Pour changer les plaquettes, nous devions démonter l'ensemble de l'outil et le réajuster. Cela prenait toujours beaucoup de temps", explique M. Enggruber. Afin d'optimiser cet effort et le résultat, Enggruber s'est mis à la recherche d'une nouvelle solution d'outil.
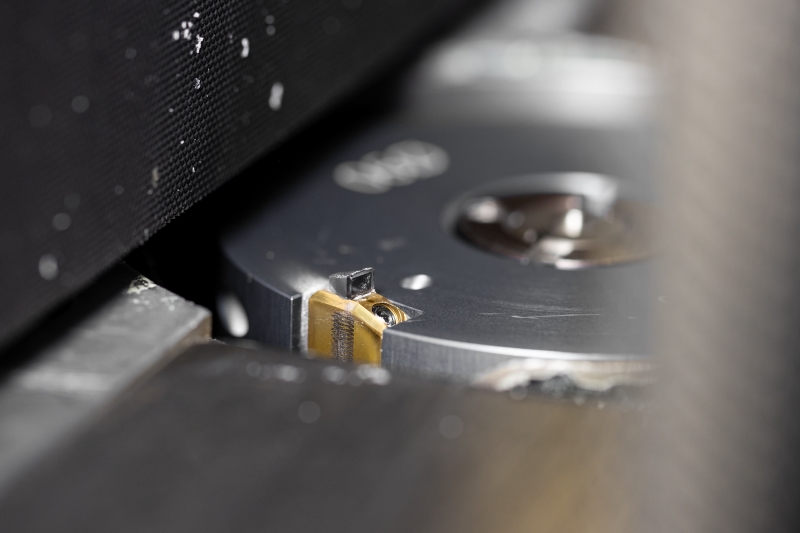
Supermini en action
Une vidéo d'usinage à haut degré de polissage téléchargée par HORN sur une plateforme vidéo en ligne bien connue a éveillé la curiosité d'Enggruber, qui a alors contacté le représentant commercial de HORN, Helmut Hoffmann. Avec Aribert Schroth, Hoffmann a analysé les problèmes d'Enggruber et a développé une nouvelle solution plus conviviale. « Grâce à notre expertise en matière de plaquettes interchangeables, la solution s'est rapidement imposée », explique M. Hoffmann. Le corps de la fraise existante est équipé d'interfaces Posalux pour accueillir les plaquettes. Les techniciens de HORN ont donc conçu une cassette Posalux dans laquelle le siège de la plaquette HORN est fraisé. La plaquette choisie est une forme spéciale du système d'outils HORN Supermini, qui peut être facilement et précisément serrée par l'avant à l'aide d'une vis de serrage dans la cassette. Il n'a donc pas été nécessaire de démonter complètement le corps de la fraise.
Les outils de fraisage ont des arêtes de coupe multiples pouvant comporter jusqu'à cinq dents et un diamètre de 120 mm (4.724"). Cependant, une seule plaquette MCD est montée par outil. Les autres plaquettes servent de prédécoupe et sont en retrait d'environ 0,1 mm. « Une seule plaquette MCD est utilisée pour produire la surface très polie, de sorte qu'elle ne soit pas endommagée par la retaille », explique M. Schroth.
Pour le polissage des bords, Enggruber utilise deux machines différentes, qui proviennent à l'origine de l'industrie du bois. « Dans notre secteur, ce concept de fraiseuse à polissage est utilisé depuis longtemps », explique M. Enggruber. Les machines n'ont qu'un seul axe pour effectuer l'opération de fraisage. Les blocs ou panneaux de verre acrylique sont maintenus par un dispositif de retenue rembourré de mousse. L'autre concept de machine est similaire à celui d'une raboteuse. Ici, la pièce est serrée entre deux larges courroies et guidée sur la fraise.
Artisanat
La qualité de l'arête de coupe de l'outil joue un rôle important dans la production de surfaces avec une finition miroir. La qualité de l'arête de coupe se reflète dans la surface à usiner. La rectification ou le polissage final des plaquettes MCD s'apparente à de l'artisanat. À l'instar de la taille des bijoux en diamant, la finition de l'arête de coupe d'un outil pour un usinage à haut degré de polissage est réalisée à la main à l'aide de pinces à affûter. Des tables de meulage à coussin d'air avec un plateau en granit massif offrent des conditions optimales pour le meulage des plaquettes. Un microscope avec un grossissement de 200x est utilisé pour l'inspection visuelle. Sous ce grossissement, l'arête de coupe doit être absolument exempte d'entailles. La plaquette obtenue a un rayon maximal de 0,0002 mm (0,000008").
Les diamants synthétiques sont principalement utilisés pour l'usinage à haut degré de polissage. Deux procédés différents sont utilisés pour produire les pierres synthétiques. Dans le procédé HPHT (High Pressure, High Temperature), les diamants sont créés sous haute pression et à haute température. En d'autres termes, il s'agit d'une méthode presque naturelle, qui ne s'étale pas sur des millions d'années mais sur quelques heures ou quelques jours, selon la taille souhaitée. Dans ce processus, la poudre de graphite pur est transformée en diamant à une pression de 60 000 bars et à une température de 1 500 degrés Celsius (2 732 degrés Fahrenheit). Les diamants issus de ce processus se caractérisent par une couleur jaune clair, due à la réfraction de la lumière par les atomes d'azote incorporés. La longueur maximale de l'arête des pierres synthétiques est de 10 mm (0,394"). Des dimensions supérieures sont théoriquement possibles, mais ne seraient pas rentables.
HORN mise sur les diamants MCC, encore plus purs, pour équiper les outils MCD. Ces pierres monocristallines sont créées par le procédé CVD. Différents gaz, principalement du méthane, sont utilisés comme source de carbone, qui se dépose pendant le processus pour permettre au diamant de croître. Les diamants se caractérisent par leur couleur cristalline ou légèrement brunâtre, en fonction de leur épaisseur. L'un des principaux avantages de ce procédé est la longueur des arêtes des pierres qui est possible. Il est ainsi possible de réaliser des outils longs avec des arêtes de coupe de 30 mm (1,181"), par exemple. Auparavant, il fallait utiliser des diamants naturels pour de tels outils, ce qui n'est pas pratique en raison de leur prix élevé, de leur rareté et des inclusions naturelles.